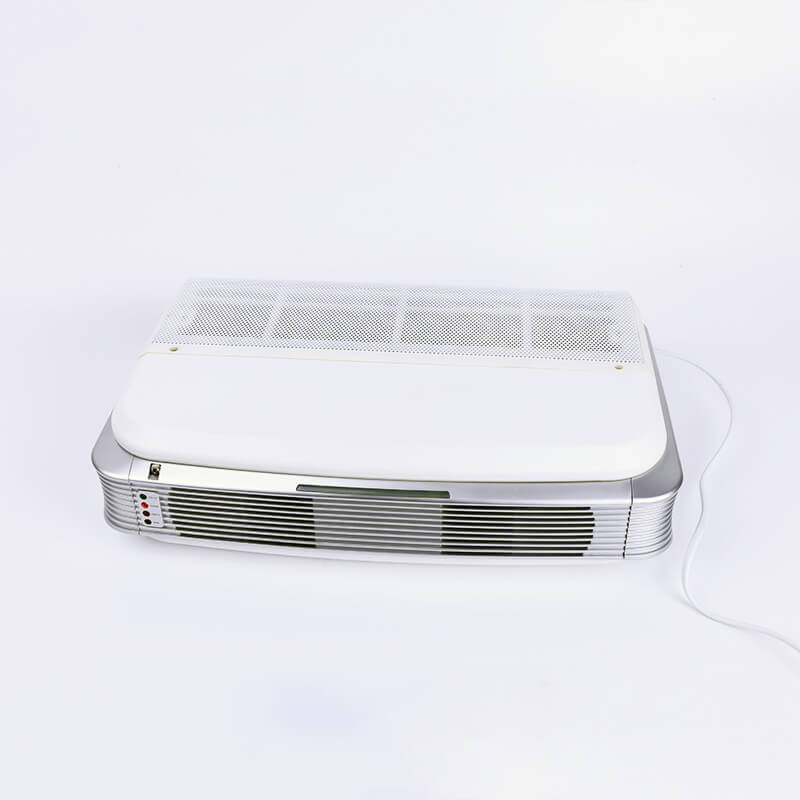
The key first step is to find the right pump--a simple old-
Is one of the past standard design.
I have a brand of 2060. Car Zone (
Auto parts chain stores)
$10 and perfect.
You want a simple cheap pump1)
The shaft of a plastic pipe with a diameter of about 1/4 "or so, rather than a diameter of 1/2 (2)
Unscrew the screw or the top of the cylinder that can be loosened by unscrewing a few small screws (3)
Rubber plates and metal plates fixed at the end of the rod (
Opposite the handle)
Use nuts so you can take them off and reverse them (4)
Metal fittings for hose connections, with six
Side base, screw the screw like a nut.
This is the hose rewind for connecting the hose and the check valve we need to remove (5)
Reasonable distance and large diameter (For bicycle pump);
The thin pump will be slower and (6)
No pressure gauge.
Pumps with pressure gauges usually use different types of check valves, and there is air space around the pressure gauge connection, which may affect how much vacuum you can pull after the conversion is complete. (
You can solve these problems, I do, but it's easier to get a negative answer. frills pump. )
If there is a car area near you, go find a 2060 slimeA "Floor Pump";
It's cheap and you will be satisfied.
Otherwise, take a look at the picture in this manual and try to find a pump that is very similar. (
I am not in contact with Auto Zone or Slime and there is no reason to think that other brands are not that good, but if you are using exactly the same pump, you should have no difficulty as instructed. )
Looking for "ground pump" in the car parts store is better than looking for "bicycle pump" in the bicycle store.
You also need:1)
4 feet "three 1/4 of ID.
Woven PVC hose. (
Lowe sells for 30 cents 1 feet in the plumbing department, so you want a dollar or so worth. )
This is a transparent flexible tube with woven steel bars;
Unlike some other small hoses, the small diameter is very beneficial to the vacuum. (2)
Check valve with Hose Hook End, 1/4 I can be installed. D. tubing. McMaster-
Carl sells these online.
About $4 for me. 00. (
Part number 6079T53 from)(
Some people use aquarium check valves for $2 at pet stores.
I tried, my leak, limit traffic a bit more than I like, but some people are happy with them.
You need to use smaller ones if you go this way-
The diameter of the connecting hose;
Let me know how it works for you. )(3)
A small hose clip.
I bought mine for 25 cents at a local tool store, but you may have to buy a 2-or 4-
Pack in most hardware or auto parts stores and pay a dollar or two.
You also need some tools:1)
Adjustable wrench or non
Adjustable fitting for hose fittings on pump. (2)
Something that can cut thin metal, such as tin scissors, pliers, Hacksaw, or rotating tools. (
You can use a file and a pair of pliers, even just some needles --nosed pliers. )(3)(maybe)
A power drill with a 1/8 bit for drilling a little bit of metal, or 2060-
A screw and a screwdriver.
The rag or paper towel is good because you will handle greasy things.
To reverse the piston disc, screw down the top of the cylinder and pull out the handle all the way so that the piston disc can be detached from the cylinder ----
Be careful. it's greasy.
You don't want to lose grease and put it on something else, so support the shaft with something to keep the piston disc away from your work area.
There are paper towels or other convenient things.
Note that the piston disc is actually a shallow cup shape with a lip around it.
The lip pops out in the descent stroke and is sealed on the cylinder. Now(1)
Unscrew the nut at the end. (2)
Pinch the rubber and metal plates together and pull them down from the end of the shaft. (3)
Turn them around. (4)
Put them back on the axis. (5)
Replace the nut and tighten it with tight hands.
Now you need to put these things back in the cylinder and you don't want to scratch the piston disc at the inside edge of the cylinder sharp, so :(6)
Pinch the rubber plate into an oval shape from the side ,(7)
Tilt the shaft and disk about 30 degrees relative to the opening end of the cylinder and insert it into one end of the Oval, and (8)
Gently place the rest of the disc into the cylinder and push it inward, pulling the shaft straight no matter where it seems to grab at the edge.
Now you can wipe the dirty oil off your fingers. (9)
In some straight push handles, and (10)
Screw back to the top of the cylinder.
You're half done.
Now use the wrench to unscrew the hose fitting from the bottom of the pump.
Exhaust check valve in hose accessories;
You need to dig it out so the air can flow freely into the pump through it.
But first you need to get the hose off and find the fitting to modify it.
There is a thin metal curl at the end of the hose to clip it on the fitting.
You need to get it off so you can get the hose off.
Cut thin metal with tin scissors, pliers, rotating tools or any tool that can cut thin metal. (
You can even take it apart with a small screwdriver and a needle --
Use some effort and nose tongs.
Pry and bend, take it apart a little bit. )
Once you get the roll edge off, remove the hose from the fitting.
You will find a "hose Rewind" there"--
A hollow cylindrical drill that extends the hose up with the horn part to help it hold the hose from the inside.
Now double check the hose fittings.
Inside is an oval cavity with a small metal ball that can move back and forth.
When it is sucked to the pump on the upper stroke, it seals, but when it is blown to the hose on the lower stroke, it does not.
This allows air to flow but not.
This is the so-called "ball check valve", which is built into the Hose Hook fitting. (
When you tilt the hose rewind down, you may barely see the ball. . .
It almost rolls to the end of the hose rewind and stops briefly when it hits some extra metal debris, which blocks the end of the hole. )
To get the ball out, you need to make the hole as big as the ball all the way to the end of the rewind.
The easy way to do this is to drill holes with a 1/8 drill bit;
Just drill into the hole and take any extra pieces of metal that hold the ball and you can roll the ball out.
My mucus 2060
A, easier than this.
I noticed a couple of metal strips opposite the end of the hose rehook that just bent inward to make the fixing parts.
All I have to do is bend them out again.
I do this by inserting the screw at the end of the inverted hook, turning the screw with a screwdriver, and holding the accessory with a wrench at the same time.
The thread of the screw grabs two curved-
Pull them out with metal sheets, enough to make room for the ball to come out. (
For other pumps that are generally similar to old pumps-
School design, you may need to drill the hose back hook to make the hole large enough to release the ball. )
Once you get the ball out, check if you have holes through the fitting.
There may be a piece of rubber that needs to be removed.
In my case, I knocked a few accessories on the table and a small piece of rubber fell out.
If you have pumps of different brands, you may need to drill your pump to tear the rubber and blow the drill out.
Direct drilling installation is not difficult, it may be a good idea anyway if you want to go to trouble. (
See the next step. )
No matter what type of check valve is inside, just drill through it and be sure to help remove it.
To reduce the resistance to the airflow, I decided to make the holes on the hose fitting a bit larger.
This doesn't make much difference in most cases, because for any substantial vacuum level, the resistance there is usually very small relative to the difficulty you have to pump.
It does make it a little easier to quickly pump larger volumes of air at lower vacuum levels. (
Just like when my vacuum cleaner starts to evacuate the vacuum bag or the vacuum tank. )
In any case, I'm just going through the existing holes with a 1/8 bit.
As with drilling metal, you should do this with small spray holes at fairly low rpm, and often pull out the drill bit to let the drill cool.
It took about a minute to unfold in a few minutes and drill holes from both ends while holding the fittings firmly with a wrench. (I use titanium.
Coating from port freight but very cheap bit. )
If you drill too fast, or drill too long, you just heat things up and pull the drill bit faster.
After drilling, blow out the metal scraps.
You don't want them to enter the pump.
Screw the hose fitting back to the pump and tighten it manually
Tighten with a wrench.
Now cut off a short hose, about inches or so long, and put it on the hose back hook.
The length of the hose should be sufficient to accommodate the back Hook End of the back Hook and check valve, but not too long. (
It could be an extra inch. )
Any extra space between the pump and the check valve will reduce the vacuum level you can pull, so don't use a long hose here.
If you use a 1/4 woven PVC like me, the hose may be perfect for sealing but not very tight, it's a good idea to put a hose clip around it.
This will ensure that it will not lose its seal and will not slide. (
Under a vacuum, it may not lose its seal because the vacuum will suck it inward onto the back Hook;
But if it slips away, you get washed away. )
Now connect the new check valve to the back hook :(1)
Make sure that the arrow on the check valve points to the pump so that it allows air to flow into the pump but does not return through the intake. (2)
Insert the appropriate end of the hook into a small number of hoses.
It should be comfortable;
Work in most ways.
Upon completion, you can connect the long remaining part of the hose to another hook in the same way;
The other end is what you attach from anything you suck.
Now you have a vacuum pump. Try it out.