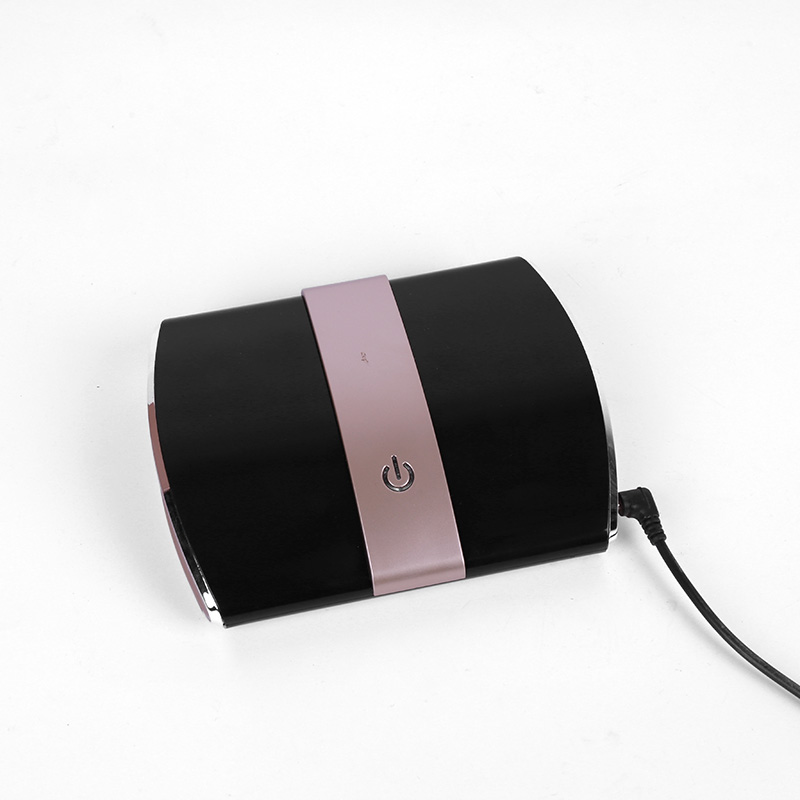
A warning to the weak-willed!
Basement renovations can be patient for you, or it can be patient for your colleagues
Residents, and your credit card!
That is to say, it's fun too!
After all, who doesn't want to break things with sledgehammer, fill the room with concrete dust, or paste huge foam on the wall?
Yeah, I can't remember anyone.
This is a huge structure with over 430 photos for you to watch.
The different stages of the decoration will be separated by the title page, in which you will find a list of tools you may need and materials you may use.
As needed, you can feel free to use any or all different parts in your own decoration.
Statement now: I am not the general contractor and do not have any building training.
However, I am a very convenient person. I read a lot of books.
Website and got a lot of help from my elders.
The information displayed in this structure is as accurate as possible, and it is likely that nothing will go wrong.
If you're not sure what you're doing, stop and step back and take a few minutes to think about it.
Read the instructions again or find a second opinion.
Now, grab your sledgehammer and remove the saw and it's time to start!
Section: planning and permitsdemotionfoundation inspection and repair, and waterproofinginvestment-
Put the sleds down in the shelving floor slab and TrimFinal steps and conclusion OK and you won't need them for a while.
Instead, take a tape measure, some chart paper and a pencil.
It's time to make some plans.
First, draw a scale diagram of the space you plan to renovate.
Includes outdoor walls, interior support walls, existing doors and windows, existing plumbing works, plumbing fixtures, and any other non-moving objects in the room.
You may not touch these (
I won't tell you what to do! )
So you have to plan around them.
Next, you have to consider what the new space will be used.
Do you want a bathroom?
Extra bedroom?
Maybe a workshop or an office. . .
Take the time to really think about what you want to build there.
After all, it's more or less permanent, so you want it to be a useful space for a long time.
You should also resist the urge to split the basement space into many small rooms --
It will eventually feel like a dungeon.
Also keep in mind that each type of room has some requirements specified by the local building code that you must follow.
For example, a large window may be required for the bedroom to exit (emergency exit)
If there is no secondary exit in the basement.
Consider these requirements when making a plan so you don't get stuck later (
Or worse, get a failing score from the construction inspector! )
In this structure, I will take my own transformation as an example.
I start with a space of 11x22 feet which is divided into two rooms, one workshop and one empty room.
Well, it's empty except for a rather quaint toilet stall!
Before you start decorating, it's important to know what you're doing, whether it's money or time.
It is also very important that you decide in advance whether you are capable of doing the job --
If not, you should hire a contractor or at least get some help from someone who knows what you're doing.
If serious structural problems are encountered (
For example, the foundation is cracked)
, You will have to have the professional fix them before proceeding with the renovation.
The cost of the renovation may be more expensive than you planned.
Most likely, you will need more 2x 4S, more drywall, more glue and a few boxes of screws.
On the good side, you just need to buy what you need and no longer need it.
I will estimate the cost in detail in each section, but if you plan a full renovation like I did, please be prepared to spend thousands of pounds.
Also, don't forget to take the cost of the tool into account.
If you have a well-stocked workshop then the cost may be negligible, but you will have to get more if you only have a few screwdrivers, hammers, and electric drills.
Luckily, now is a good time to go out and buy all the fun power tools you 've always wanted!
In most cases, it would be cheaper to simply buy this tool than to rent one, especially if your renovations span a few months.
Finally, I strongly object to you starting to decorate unless you can afford to do so.
Don't buy anything with a credit card, unless you have funds in your bank account that pay your bills on the same day.
One of the worst situations you can get yourself into is half
After the renovation, there is nothing in the bank.
If you are like me, you have very little spare time.
Between working and helping raise a young daughter, I'm lucky if I can get an hour for myself these days --
Usually I have to be very quiet as little munchkin is napping!
With this in mind, you have to be prepared for two things.
First of all, the space you are developing will not be fully available in a few months.
Second, you won't have much time to do other things when you decorate.
Of course, you can work in stages, but the space won't work until the floor is installed, the paint is on the wall, the outlet board is screwed --
Everything is at the end.
Oh, one more thing.
It is important that you prepare your colleagues. dwellers (
Especially the spouse or other important person)
For things in the store.
Make sure they understand that their house will be torn apart for a while.
Make sure they know you'll track dirt in their house, drive to Home Depot often and stay up late after DingTalk.
Renovations will have almost as much impact on their lives as yours.
Are all your plans planned? Check!
Do you get permission from your other half to spend thousands of dollars in a local hardware store? Yay!
It's time to pick up the sledgehammer, but one more thing to do: get a building permit.
Where I live, building permit is required for basement decoration.
Without it, the city will force you to tear everything off if there is a problem, and your insurance company can refuse to insure your house.
Fortunately, at least where I live, it's easy to get a permit.
All I need is a scale chart of planned renovations showing the location of the walls, doors, windows and pipes.
The size of the windows and doors and the height of the ceiling also need to be marked.
Depending on the size of the renovation, the license will cost you several hundred dollars.
Later, when the building inspector comes to check your work, he/she will want to see the permit.
They may come three times, once in structural engineering, once in plumbing and electrical engineering, and once in final inspection.
Of course, you can continue the renovation without a permit, but you can do it yourself (legal)peril.
Okay, now is the fun time!
Tools you may need: sledgehammer-
Used for the removal of concrete block walls, for the separation of 2 x 4S, which usually hit the material very hard. Large Pry Bar -
Used to pull nails and pry small crowbars from the drywall-
Sledgehammer nail-
Used to pry nails, pry poles, smash drywall, remove saw
For cutting 2x 4S and other frame members
For removing the screed cutter
Garbage bag for cutting electric Wikia stpan-
Clean the vacuum using a fine particle filter-
Net angle grinder with brick and stone plate-
For smooth concrete fan
To breathe fresh air and blow dust from windows, eyes, hands, feet and breath protection
In order to avoid the pain of building injuries, depending on how far the space has been "done", you may need to rent a large trash can for all the pieces.
Smaller jobs, or rooms with few jobs done to them, may only require a lot of industry-
Strengthen garbage bags.
Find out from the city what you can and can't throw away in regular garbage.
On the most basic level, demolition includes a basic rule: Break things until it lies on a pile of things on the floor.
But we are not so primitive, so there is a more civilized way to solve this problem. 1.
First remove anything from the space that is not nailed.
The only thing you are tearing off that should be in the room should be the tools you need to work. 2.
Power off the space.
Turn off the power supply at the circuit breaker or fuse panel. Better yet -
Turn off the power of the house and completely remove the space you are working from the circuit.
This will ensure your safety when you hit the wall, remove the electrical appliances and cut off the wires.
After power failure, walk around with the circuit tester to make sure there is no power supply.
From now on, your power tools will run on extension lines inserted elsewhere in the building. 3. Start smashing!
Move everything to the concrete walls and floors
Do everything well.
It also allows you to check if there are cracks and leaks in the Foundation
The problem you will want to solve before going further.
Most of the things you tear off cannot or should not be used again.
Here's a short list of things you might remove and if you should bother to keep it: Drywall: Throw it away! Trim (Substrate, etc)
: Please keep it if it is in good shape, only long chip power outlets and switches: please keep it if they are the style you want to use.
Throw away old dimmers
Fixtures: throw away or deliver on FreecycleElectrical wire: Keep the updated plastic only-
Jacket wire, only long pieces.
2x4 s and other structural things: keep the long part and remove the old nails.
Note that these components should not be used in new buildings and they are only suitable for support and firewood.
Old Nail, screw: Throw it out!
Concrete: Throw it on the old floor: Throw it out in a safe way!
Old insulation: Throw it away in a safe way! 4.
Clean up your mess!
Throw all your trash in a garbage bag or park in a big bin in the driveway.
Clean and vacuum all the saw dust and dry wall dust on the floor.
Store any items you keep in a safe place.
Now that you have stripped the walls and floors, you can check for leaks and cracks in the foundation.
These problems will only get worse over time, and if they are not solved, they will lead to serious headaches.
Here are some things to find: Fracture of line (or worse! )
Running along the wall
Cracks in floor molds (
Black, red, greenit's all bad! )
If you find any issues similar to those listed above, please call the professional to check!
They are all signs of Foundation movement and moisture penetration.
During the demolition, I managed to pull a few pieces of concrete from the wall.
This happened where the previous owner used concrete nails to attach the wooden strips directly to the wall.
The damage to the wall was small, so I patched it with some concrete patching material.
There were also a few holes in the old screws and I filled them in too.
Fortunately for me, the former owner has painted the concrete wall with moistureproofing paint.
If your walls and floors are bare, then I would recommend doing so before any walls are erected.
A few months before I started the renovation project, I had an energy assessment of my home.
The results were surprising, especially in the basement.
It turns out that most of the heat coming out of the house is left through the walls of the basement, especially the part between the ground outside and the main floor.
Only 18 inch of the concrete wall above grade is the reason for my 25% heat loss!
It is clear that it makes sense to insulate the walls of the basement.
Unfortunately, the walls of the insulated basement are not as easy as hitting the glass fiber.
There are moisture issues that need to be addressed, and if you don't do well then you have the potential to build a perfect small habitat for growing toxic mold.
Theory: concrete, although it can crush your feet most effectively, it is not solid.
It is porous to water and also conducts heat well.
Dry walls, steam barriers, and fiberglass insulation also allow the movement of moisture, albeit to a lesser extent.
It is important to keep this in mind because it means that moisture can enter from both sides of the inner wall
Wet ground from the outside, wet air from the inside!
The goal here is to minimize the accumulation of moisture between the concrete wall and the inside of the wall you are going to build.
This means that you have to do two things: to prevent the damp indoor air from reaching the cool concrete wall (
Thus preventing condensation)
To prevent the accumulation of moisture in the concrete into the wall.
After a lot of research, I found the answer.
What we have to do is paste the foam sheet directly onto the wall to form a sealed barrier around the outer wall.
The damp and warm indoor air will not be able to reach the cold concrete walls, although the moisture from the concrete penetration is stopped because it has no air gap to evaporate.
In addition to this, foam Inhibits mold growth and increases further protection.
No steam barrier required!
How much insulation is used?
In my case, I used three layers of insulation.
I started with 2 inch and 0 two layers of foam insulation.
5 inch thick, staggered to limit air flow to the maximum extent.
Once the bolt Wall was installed, I stuffed 3.
5 inch glass fiber insulation.
This provides an R-
The value of the half part of the wall is 27, and the value of the lower half is R13.
Tools: big caulking gun-
Hand Saw for dispensing foam adhesive-
For cutting foam board and fiberglass war knife
For cutting foam sheet measurement-
For measurement, of course!
Carpenter Square-
For accurate measurement of markers-
Used to draw cutting lines on foam material: 4x8'2 "thick foam plastic sheet, as required 4x8'0.
5 "in accordance with the requirements of the steam barrier sealing tape, thick foam plastic sheet-
For sealing seams between foam sheet fiberglass batting, for 4 "16" on-
Center spacing, rated basement useFoam adhesive, 800 ml tubes, such as what is hollow in requiredGreat foamBefore, start to make sure the walls are clean and dry.
If you are going to expand the windows to fit the building code, then do this first.
If you have a pipe running directly along the wall, remove it a bit if you can.
You don't want to bury the pipe under the insulation.
The process is very simple.
2 "The foam board will have lips along the long ends designed to fit together.
When you measure each piece of foam, make sure the panel is aligned correctly for a good fit.
Just measure the space that the foam panel will fit and Mark anything that needs to be cut.
Try to leave the smallest possible gap between the edge of the foam board and any surface it touches.
Dry install foam board and trim as needed.
When you are satisfied with the fit, grab the caulking gun with foam glue and lay a 1/4 bead in a wave pattern along the back of the foam.
Stick the foam in place and gently peel it off again.
Let the glue "open" for a minute or two before sticking the foam back to the wall.
This process helps to adhere quickly and correctly.
Now, just work in the room and fill the entire exterior wall surface with a foam board.
If you put on the second floor like I did, the process is the same.
Measure, cut, fit, glue and stick.
When installing the second layer, make sure it completely overlaps the seams of the lower layer.
This will further reduce the airflow and improve the performance of the panel.
Take another step forward and seal all the seams with the Tuck belt.
The insulation steps are currently completed until the frame and electrical installation are completed.
After installing the bolt wall and all the wires, you can complete the insulation with a layer of fiberglass insulation.
This is not absolutely necessary, but it improves the heat resistance of the healthy R27, precisely where your house leaks the most heat.
This is one of the easiest steps to decorate.
However, you must wear enough PPE.
Put on your eyes and breath protection to make sure all your skin is covered, especially your hands!
Fiberglass can give you a rash and can be very dangerous if you breathe in fiberglass.
Cut the insulated bag with a knife.
It's compressed so be careful
It will expand rapidly!
The walls we renovated are framed with 2x4 s and 16 "spacing, so if you get a matching fiberglass size, batts will be perfect for there.
Just slide each batt between studs and be careful not to compress the batt too much.
If it doesn't fit, then cut the batt to the right size with a knife or saw and don't try to crush it.
In the space where the electric box is located, cut a gap on the fiberglass to suit the surrounding environment.
This is all about it.
Make sure you clean it up carefully after you're done-
You don't want to transfer the fiberglass particles to other clothes, and you don't want to track it on your shoes.
I suggest starting the drywall as soon as possible so that the fiberglass can be exposed to the air in the shortest possible time.
In my opinion, framing is the most enjoyable part of the process, second only to smashing things with sledgehammer.
There is some fun seeing the shape of the walls, although they may be bones.
The anatomical basic wall of the column wall consists of three components: the top plate, the bottom plate and the column.
The top plate is horizontal, extending along the ceiling, and the bottom plate is horizontal, extending along the floor.
The columns are aligned vertically, extending from the ceiling to the floor.
There are two basic methods for vertical walls.
You can build the wall part on the ground level and raise it up in place, or you can connect the top and bottom plates and install the bolts between the two.
Since the walls, ceiling beams and floors in the room where I worked were a bit uneven, I decided to use the second method to save my sanity. TOOLSHammer -
It's for DingTalk, of course. Power drill -
Saw for rotary screwdriver-
For cutting studsHammer drill
Drill hole for concrete high quality concrete drill bit
Because the one in the screw box is garbage. Tape measure-
Make sure it's a metric tag with a height of 4 feet
Make sure everything is level. Laser Level -
It's not necessary, but it's much easier to make things! Plumb bob -
Used to align the top and bottom platform handsaw-
Very few clips for special cuts
When you nail or screw on the tool, fix the bolt in the appropriate position --
Pencil, marker or something.
Just write on wood and concrete.
Protect your eyes, ears and breath
The power tools were loud and messed up.
Protect yourself! Nail Gun -
This is optional.
This is definitely faster than manual DingTalk, but it's expensive to buy or rent.
Material 2x4x8 Wood-Lots of it!
You will place one for every 16 inch and use more around windows, doors and corners.
2x4x8 pressure treated wood-
Only 10 days bright spiral nails for the bottom plate-Boxes of 'em. 2. 5 -
3 "long construction screws-
Before finishing the work with several nails 4 "long Tapcon concrete screws, fixing the bolts is useful --
In order to connect the bottom plate to the floor, the bottom plate is the foundation of all the walls you are going to build.
It will be fixed on the floor using Tapcon concrete screws, nailed and/or screwed on.
Since it will be in contact with the concrete floor, it must be treated under pressure in wet conditions.
When you choose the wood for the bottom plate, make sure it is straight, flat and without any distortion or distortion.
Before Home Depot loads each item into a shopping cart (
Or anywhere you get the wood)
, Observe along the length to find the defect.
If you find something, put it back.
In order to reduce the headache in the later stage of construction, the bottom plate (
And the roof)
Must be perfect.
* Note: do not go to buy wood with your spouse or child.
When you spend an hour or two looking for the best wood, they go crazy bored. Trust me.
The layout of the bottom plate will determine the location of all the walls, so please make sure to position it carefully.
Close the 2x 4S to the wall, and the gap between the wood and the wall/insulation does not exceed 1/4.
For long spans that require more than one piece of wood, please make sure that the wood is parallel.
In the corner, double check your angle90, 45, etc.
It's worth spending time here.
Nothing complicated here.
Measure twice and cut once with a diagonal saw.
Strive for easy cooperation without gap between parts.
Drill holes and ironing boards grab the hammer drill and install the masonry drill bit.
There should be a gauge on the side of the bit that you can use to control the depth of the hole.
In this case, the hole will be the length of the screw plus a little margin (Say an extra 1/2.
Place the bottom plate where you want, go straight through the center of the wood and drill into concrete perpendicular to the floor.
Drill the first hole near the end of the workpiece, about 6 "from the end ".
It may be necessary to pull the drill bit out several times so that concrete dust can escape.
Standing on the wood helps prevent it from moving around when you drill holes.
After drilling the first hole, use the power drill to drive in the Tapcon screw.
I would suggest using socket head bit to do this and it would be a lot less.
Don't leave it on all the time.
Again, it helps to stand on the wood and keep it flat on the ground.
Now go to the other end of the bottom plate, re-align the wood if necessary, and drill the second hole.
Drive at another Tapcon.
Now the bottom plate will not move, you can continue to open a few more screws along the length of the bottom plate.
At least, place one for every 2 feet or so.
Continue in this way with the rest of the room.
Be extra careful when aligning internal partitions
They should be perpendicular to the outer wall (
Unless you have an avant-garde plan. .
Where there will be a door, put the bottom plate just in the gap-
The part will be cut off when the door frame is finished.
Obviously, the top plate must be absolutely parallel and aligned with the bottom plate.
If not, your headache will be huge and your curse will be loud and profane.
As with the bottom plate, it is essential that the top plate wood be as perfect as possible.
Take the time to pick good pieces and later you will be rewarded with easier installation and less waste wood.
Take a moment to look at the top of your beam.
They will cross the room vertically or horizontally and attach the top plates to these beams.
This process is easy when the top plate is perpendicular to the beam.
Just screw the top plate anywhere they go through.
Where they are parallel, you will have to nail on a few small pieces of wood spanning the distance of the beam in May 1, and then attach the top plate to them.
Align the top platform this is probably one of the more tricky parts of the process.
I find that the best way to do this is to use a lead hammer or a laser level to align one end, screw in, and then align the other end.
Align using a straight line 2x4 check relative to the top and bottom plates, with a level of 4 feet relative to 2x4.
Everything is arranged at both ends, move on and push the screws into each pallet.
Move around the room and install a roof plate right above each floor plate.
Take a moment and get it right the first time.
OK, this is where everything will begin to take shape!
Most of the building codes in North America will be in-
Center column distance.
This means that if measured from the center of each bolt, each Bolt will be 16 "from its neighbor ".
Of course, this will change when you hit the corner --
You may have a shorter section.
When planning the position of the nail, it is important to remember the drywall steps.
Specifically, will you have a place to screw the drywall to it?
This is critical for the corners as you need to make sure the bolts are in place --
For the outer corner, place a Bolt at the end, and for the inner corner, place a bolt at each end of the meeting wall.
If you make a mistake, you can always put an extra spike, but why waste wood?
After remembering the placement rules, start at one end of the wall and mark the center where the first bolt is placed.
I prefer to mark the sides of the bottom plate.
Stick out your tape measure and mark the position of the next Bolt along the wall every 16 "intervals.
Your tape measure can even easily mark these intervals for you.
Now, the mark is also transferred to the top plate using a laser or lead hammer.
Measure the position of each bolt very carefully.
You don't want it to be too tight or too loose.
It's too tight. you might drop some nails (
If you can force the bolt in the first time! )
Too loose, you have to waste time on the gasket.
That's why I suggest you measure the bolts with metrics.
It's much easier to remember a precise number to mm instead of confusing with feet, inches and fractions.
Mark the measurement on the nail with a pencil or marker pen.
With a herringbone saw, the bolts are cut precisely to the outside of the mark.
It should remain upright when you put the bolt back in place, but it is easy to disassemble.
The easiest way to tighten the bolts is to first drive with a screw at both ends with a power bit.
Fix the bolt to the top with one hand and drive slowly with the screw so the Bolt does not move.
Then, move to the bottom.
After the screws are in place, quickly check the bolts with a level.
Now, you can do the job with a few nails at both ends of the bolt without worrying about the Bolt moving left or right due to hammer force.
Put at least two nails at each end, on the opposite side of the bolt.
After driving on the nail, check to make sure the bolt is at the level for the last time.
Now, repeat it dozens of times.
What do you do with all the cuts?
The ceiling in my basement is only about 6'6', so I ended up providing an 18 "deadline for each bolt.
These parts are perfect for horizontal placement between bolts!
Cut each piece to a suitable length (
About 15 years old)
And nail in the appropriate position with staggered patterns.
This is not required, but it adds a lot of structural stiffness to the wall.
Special windows and doors have special requirements in terms of frame.
Read how to deal with them in their respective sections.
We couldn't have the big, ugly back air in our beautiful room!
It will be enclosed in something called "soffit"
The frame built around the vent can be covered with a dry wall.
The same method can be used to close the steel H-
Beams, vents, water pipes and other ugly things that affect the look of the room.
Soffit is built on the ground and lifted in place.
First take a careful measurement to make sure there is a little space left between the inside edge of soffit and the vents.
Also keep in mind that the wall under soffit needs to be specially built as the top plate cannot be screwed to the ceiling
It will be fixed on the wall.
Soffit consists of 2x2 s, 2 x 4S and half inch plywood.
Start by cutting a piece of plywood that extends from the ceiling to below the vent.
You may need to place more than one endto-end.
Then twist 2x2 s on the edges on both sides of the plywood for the entire length.
This will create a rigid, fully straight cover for the surface of the vent.
Next, create a "top plate" for the wall below the vent, which will extend the length of soffit.
This top plate will eventually be supported by bolts on both sides of the vent and brackets anchored on the wall.
Between the top plate and plywood, cut the 2x4 short film placed on the top of the top plate and attach it to the back of the plywood cover.
Very careful measurements are needed here!
With the help of the assistant, lift soffit to the position above the vent and screw it into the bolts at both ends of the ceiling pallet and soffit.
It should support its own weight now.
As usual, install a bolt every 16 inch m to complete the wall under soffit.
To make the column Wall under soffit stronger, use some pieces of 2x4 to build a stand.
The bracket should be fixed on the wall using Tapcon screws and screwed on the bolts close to the top plate.
Use one or more brackets depending on the length of soffit. There you go -
Soffit can now dry walls like any other wall!
Now things are really coming together.
The walls are framed and you can start to know what the room will look like!
It's time for the next step, electrical!
Now, you may have heard from others that you have to have a licensed electrician to do this kind of work.
If you are not familiar with the basic electrical theory, maybe you should do so.
Most electrical work, however, is very simple and direct, so what you really need once the work is done is for the professional to check your work!
You can have a real electrician do it for you or have the building inspector do it for you.
Anyway, it's a good thing if it's just for inner peace.
THEORYI will show you how to connect the three most basic elements of the electrical system: sockets, lights, and switches.
In each of the jacketed wires, you will find three wires, one bare copper wire (ground)
A white insulated wire (neutral)
And black insulated wires (hot or live).
We will keep it simple and say the current flows from black to white.
Grounding wire is a safety net;
If something inside the electrical device is short-circuited, the current can pass through the ground rather than through you.
The sockets in the circuit are connected in parallel.
This means that a ground, neutral, and hot wire will be attached to each socket.
The switch is connected differently.
The ordinary single-bar switch is connected in series with the hot wire, and the neutral wire passes exactly.
Therefore, turning off the switch will cut off the current flowing to the lamp-
An important security function.
Tool rig-
Drilling Hole socket spade position-
For drilling holes with large diameter, wire can be installed by Cutter/stripping
For cutting cables and stripping insulated screwdrivers-
For the installation of the electric box and the fixing of the wire to the terminal
For installation of electric box and connection cable connector 14 meter 3-conductor (
2 conductor grounding)
Cable TV junction box for home use-
Socket and switch octagonal junction box-
Cover plate for branch cable and some fixed octagonal junction box
Box for covering yellow and orange Marrettes-
Used to connect the ends of two or more wires together (
Note: Marrette is the brand name)Cable Clamps -
Used to connect the cable to a studs10 nail or 1 "construction screw-
Connecting the electric box to the socket and where the switch will go is sometimes harder than you think.
You want to make sure the outlets are placed where needed, the switches are in a logical position and anyone can find them in the dark.
In their 50 s and 60 s, people don't have a lot of electronic products.
Usually, one or two outlets in the whole room are enough.
These days, our eyeballs are connected, so more outlets are needed.
In my decoration, a socket is placed about every three to 4 feet metres.
I'm not going to use it all, but they are ready if I need.
Except for some special cases, sockets are usually placed about 1 feet from the ground.
In my new workshop, tables are arranged on the walls, so the sockets are about 1 feet higher than the table top.
In the bathroom, you may want to place a socket above the sink so you can insert a shaver or an electric toothbrush.
Switches are usually placed 4 feet away from the ground.
To control the different lights in the room, you may only need one switch, or a whole set of switches.
If there are multiple entry points in the room, you may want to connect a switch near each entrance.
In this case, you need to use a double-bar switch (
Also called Threeway switches)and a four-
Conductor cable (
White, black, red).
Lighting the lights you choose for your project may be equipped with special mounting hardware like I did, or they may simply be connected to a standard octagonal junction box.
Depending on the style, the lamp can be installed on the wall or ceiling.
When you decide where to find your lamp, you must first decide what the purpose of the lamp is --
Is it meant to illuminate a particular area, or is it just an emphasis on lighting?
Consider the location of the furniture, doors, shelves and work areas after the completion of the room and plan ahead.
There may be several spikes on one side of the junction box-
This is the side opposite the bolt.
Line up the box so that the opening will stretch out the bolt edge of about 1/4.
Hammer it in so that the box can stay where it is, and then make it permanent by nailing a few nails in the holes at the top and bottom of the box.
Octagonal junction boxes can be purchased with or without spikes.
In this case, use construction screws instead of nails once the box is in place.
Since you can easily enter the inside of the box, you can use shorter fasteners and faster screws.
If your lamp uses special hardware, please follow the instructions provided when installing the box.
In my renovation, I used the flush mounted pot light, which was connected directly to the pallet using a special hanger bracket.
With the junction box, you can run the wires.
Before starting, I suggest drawing the path the wires will go.
You can use a copy of your blueprint for this.
Try to make the path more efficient-
This will save you time and money.
In my renovation, I used the junction box installed on the ceiling to divide the power supply from the circuit breaker panel into two circuits: one for the socket and one for the lighting.
From there on, the sockets are all daisy chains to keep the minimum amount of wire usage.
The wiring of the lights is a little different-
The wire goes through the switch before connecting to the light.
They are also daisy chains.
Drilling you need to drill a few holes here and there so that the wires can go through the bolts and the top plate.
Using the wiring diagram, find every place where the wires must go through the bolts and drill holes there.
If possible, try drilling 1 inch holes from the back of the bolt.
The holes you drill should be large enough to hold the wires that go throughand no larger.
In most cases, you can unplug a long wire from the reel without cutting off the reel.
Start at one end of the run (
For example, outside the export box)
, As you go, pass the wire through any drill along the nail.
Try to avoid twisting wires if possible.
Leave around 1 feet extra wires at each end of the run.
Then, cut off the cable from the reel.
The junction box will have four or more labels, two on the top and two on the bottom, and you can bend to pass the cable.
Bend the label closest to the incoming line and pass the wire through.
The integrated fixture inside the box can then be tightened to secure the wires in place.
Fix the wire with the wire clip in the junction box and you can start using the wire clip to pin the wire to the bolt.
Put the first one a few inches away from the junction box, every 12-
After 16 inch
Where the wire turns, nail a clip at the beginning and end of the turn, leaving a small amount of slack on the wire so that it does not have to form a sharp angle.
Try to keep the wires flat and avoid distortion.
Work along the length of the wire until you reach the end of the wire.
Please note that you can run the wires parallel along the bolts, but I do not recommend running more than two wires on one side.
Also, do not stack the wires and do not use a clip for both wires.
Running the wire from circuit breaker PANELI usually starts with this wire.
This is usually the longest run, especially if you have to go through the house.
In my case, I had to go fishing through the pallet and through the rec room ceiling, and the task was done with two long 1x1 s with bent nails at the end.
You can connect it to the socket and switch in the room you are renovating, but don't connect it to the breaker panel. FINISHING OFF -FOR NOW.
Since the socket itself will be placed at the top of the drywall, you can't connect the socket or switch yet.
Now, just roll the cord that hangs on the outside of the junction box back to yourself, then stuff them into the box and leave.
After the drywall is turned on, you can install the socket and switch.
The Outletthe socket will have five screws, two on each side and one on the label near the bottom.
The screws at the bottom are grounded.
The pair of screws on the right is "hot" and the pair on the left is "neutral ".
"You can also distinguish the difference between the two by observing the size of the outlet hole --
The smaller slots are hot and the larger ones are neutral.
This round hole is the ground.
You will connect the black line (s)
The hot side, the white line (s)
To neutral, ground wire (you guessed it! )ground.
Bring the wires and back to the edge of the plastic jacket all the way to the outlet box.
Once you're good at it, you don't need too many wires to work.
Stay a little more if you're new.
Cut off the black and white wires to highlight the outgoing box about 6.
With stripping, the insulation is stripped at each end for about three quarters.
Cut off the ground wire and make about 8 "stand out from the wall.
Bend a small ring with a needle nose clamp to the end of each wire including the ground.
Feed each wire end under the appropriate screws and tighten.
When you are done, there should be a minimum of copper exposed to the edge of the screw.
If there are extra wires, trim them down with a side cutter.
With socket wiring, you can plug the wire back into the socket box and screw it into the socket using the built-in screwsin screws.
Make sure the ground wire does not touch the neutral or hot screws on the side of the socket!
When you tighten the socket in place, make sure it is perpendicular to the floor.
There are only two screws in the normal single rod switch. The hot (black)
The wires that pass in the live wire will be connected to one screw and the hot wire from the outgoing wire will be connected to the other screw.
White and ground wire are simply connected together at the endto-
Finally, take advantage of marrettes.
This process is almost the same as tat connecting the socket.
Peel the plastic jacket back and cut the wire to about 6 inch.
1/2 "per end, but only put a ring on the black wire.
Start with white and ground: hold two white wires side by side and align the tip.
Twist an orange marrette on the wire until the wire starts winding each other.
You should be able to pull the wires without pulling them out of marrette.
Repeat the ground.
Then, put the white and ground wires back into the switch junction box.
Now fix the two black wires on the screw terminals on the switch.
Plug the black wire into the switch box and screw it into the switch.
Make sure the ground wire does not touch the screw terminals on the Switch!
Depending on the light you have installed, the connection method will vary.
Some lights, like basic single
The bulb fixture is designed to be mounted directly on the octagonal junction box.
They have screw terminals connected with white and black wires, and the ground wire is connected to the screw terminals inside the junction box.
Then, fix the light on the junction box using the included screws.
Other lights are designed to fit on the same junction box, but there are wires instead of screw terminals.
In this case, it's just a matter of color matching-
White to white, black to black.
And ground to ground.
Use marrettes to tie the ends of the wire together.
Then, connect the fixture to the junction box using the hardware provided.
This hardware may vary, so please follow the instructions that come with it.
I used their own dedicated junction box for embedded basin lights for my renovations and installed them directly on the fixtures.
Use a special bracket to connect to a fixture on the ceiling beam.
If your light is like this, then follow the instructions provided.
During my renovation, there is no need for me to do too much work on the plumbing works.
I installed a second cold air return (
Because there is no basement)
, And several registration covers have been installed.
When using sheet metal, the usual rule is: measure several times and cut carefully. TOOLSShears -
For cutting sheet metal "bite" knives
For tricky cutting of metal plates, you can't do it with a shearsPower drill bit --
Used to drill starter holes in existing pipe tape measure
For measurement marking-
Sheet metal materials for pipe engineering flat metal-
Pipes are made of pre-formed raw materials
Make pipe workpiece-
For installation of a new vent or pipe registration cover-
Cover and protect ventsAluminum tape-
It's not cloth! Straps -
In order to ensure ventilation pipes, beams and studsScrews-
When the energy efficiency inspector checked our house, it was better to tie the straps to the wood and he advised me to add cold air back in the basement.
This improves the flow of air throughout the house.
In the summer, cool basement air can be pumped to the upper floor to help the house cool down.
In the workshop area I decorated, the main cold air return pipe went straight through.
I decided to install a vent at the end of the pipe, as far away as possible from the sawdust source.
Before closing the pipe on the sofa (Description later)
, I did the following: first, measure the area where you want the vent to be.
There are many different sizes of vent covers to choose from, just choose the first best one.
Holding the vent in hand determines how big the opening in the pipe should be.
In my case, this is the area in the center, not the edge outside!
Transfer these dimensions to the pipe using a permanent mark.
You need to install a small pipe that extends from the edge of the main pipe to the vent (
This in turn falls on the top of the drywall).
This way, you can install something on the pipe, and you can cut the label on the supervisor.
Inside the rectangle drawn on the pipe, draw a smaller rectangle of about 1 "on each side.
Then, draw a line between each of the four corners.
Use the drill bit to cut a hole in each corner of the inner rectangle.
Then, cut the knife with scissors or bite (
Which works best for you)
, Cut out the smaller inner rectangle.
Then, cut along the diagonal that connects the two rectangular corners.
Fold the label out as neatly as possible and try a clean 90 degree bend.
Cut a small piece of metal plate as a bridge between the main pipe hole and the vent.
It should be placed closely outside the label and surrounded all the way.
You may want to leave this step before you are ready to install the drywall.
Now, as described later in this manual, close and install soffit around the pipe.
When the dry wall transfers the part where the vent is located, the dimensions of the vent opening are transferred to the surface of the dry wall.
Then cut the opening.
Install the drywall in place and slide the small pipe you made before in place.
Everything should be arranged.
Screw on the wall
Using an aluminum strip, attach the label to the inside of the small pipe.
Try to keep the tape smooth and make sure to seal any air gap.
Finally, connect the vent cover to the top of the vent hole.
Welcome to the most challenging part of the decoration.
I must admit that before starting this project, I had little knowledge of how to dry the wall, and at best I was a newbie.
Everything I learned (
Most of the work, in fact)
It can be attributed to my father-in-law who has been doing it for many years.
The first is some background.
The drywall is basically a plaster wrapped in paper.
It has many different thickness, 1/2 "is the most common.
The 5/8 "drywall is often used in the bedroom because it can resist the spread of the fire for a longer period of time, thus giving more escape time to any occupant.
There are also different varieties. The most striking thing is the "green plate" that is moisture-proof "(
But not waterproof).
Although not in the actual shower or tub, it is used in the bathroom.
The drywall is fixed to the nail wall with drywall screws, and can also be directly glued to the foam insulation.
It is usually 48 inch wide (
The width of three DingTalk)
Anywhere from 8 to 12 feet long.
The gap between the drywall panels fills the drywall compound, which is a fast
Smooth dry plaster easy to polish.
In this renovation, I chose to use the normal old 1/2 drywall on the walls and ceiling.
Tool knife-
For cutting and cutting of drywall saw
A small, positive saw for cutting a drywall power drill-
Screw in the dimpler position of screwsDrywall gypsum board
A special drill for drywall screws that creates a recessed "dimples" around the spiral tape around the drywall surface"
It should be obvious now! Drywall T-square -
Used to draw completely vertical lines on dry walls
Used to raise the drywall from the floor during installation
A "T" shape made of 2x 4S to support a drywall mounted on the ceiling.
It's important if you work alone!
Drywall trowels-3 ", 6" and 10"
Dry Wall for laying small and large corner trucks-
Neat corner metal scissors
For cutting all kinds of grinding plates-
For grinding dry wall composite vacuum with fine particle filter-
For breathing protection-
Because it's not good for you to suck in dry wall dust. Laser Level (
Type of vertical line on the wall)-
This is a very useful device!
Material wall-
All my stuff is 1/2 ordinary.
It is estimated that there will be one for every 4 feet pieces, plus some extraDrywall screws
About 30 per 4x8-35 screws.
Gypsum Board-
Get something "dust control" and use it better. Durabond 90 -a high-
Strength drywall repair compound for filling large gaps and covering corners to support drywall tape-
Used to bridge the gap between drywalls and give drywall compounds something to hold on to, I actually think this part is interesting.
Measure the space, cut the dry wall panel to fit and screw it in place.
Well, it's a bit more tricky than that. ; )
I will explain first how to install a dry wall on the wall, although you usually start with the ceiling.
The reason for this is that in the corner where the walls and ceilings meet, it is much easier to install a dry wall on the walls to perfectly install.
Therefore, the drywall on the wall covers any gaps left by a piece of paper on the ceiling.
Before installing the first drywall, take the time to plan where you will start.
Most of your walls are most likely not a precise multiple of 4 feet, so at least one drywall should be shortened to accommodate.
Ideally, the cutting edge should be placed in order to bury it in the inner corner.
Instead, try to line up the beautiful factory
Finish the edge at the outer corner.
Measure the entire wall first to determine how many sheets of paper are needed.
Taking this number into account, write down where the shortened paper will be (
Ideally in the corner).
It doesn't matter that you can make this paper first or last.
Lay a dry wall on the floor.
Make sure the floor is clean and you have plenty of room to work around.
Using a tape measure, first determine the exact height and width of the part of the wall to be covered.
Please note that 16 "on-
Center column wall structure, a whole dry wall should be perfectly aligned with the column, and the edge of the dry wall is aligned with the center of the column.
Transfer these measurements to the finished side of the drywall.
Reduce the height measurement by about 1/4 ", so the drywall can be lifted from the floor.
Next, find any exit in that part of the wall and mark out where the exit needs to be cut.
There are two main ways to cut dry walls.
Each has its benefits.
The first method is to score along the cutting line with a tool knife so that the paper and a little plaster can be cut.
Sharp blades are essential.
Then, break the dry wall panel along this line.
It's easy to happen!
Back the paper with a knife to finish cutting.
This leads to a relatively clean line.
The downside is that you can only do straight lines and the cutting must be from start to finish.
The second method is to use a drywall saw.
Simple operation-
Just cut the board with a saw.
Internal cutting (
For example, dig a hole for the exit)
You don't even need to drill holes-
Just pass the saw point through the drywall.
The drywall saw also allows you to cut corners and curves in the drywall, but at a reasonable price.
The edges are more rough and confusing than the scored wounds.
This step of installing drywall becomes easier by using laser lines.
This is a simple gadget that can draw a perfect horizontal vertical line on the wall.
Before attaching the drywall to the wall, mark the position of all bolts on the floor with marking or tape.
Place the two gaskets on the floor where the drywall is going, and then lift the drywall in place.
It should be mounted evenly on a corner or adjacent drywall board and flush with it.
Check whether the outlet and vent are suitable and trim if necessary.
Increase or decrease the thickness of the gasket to fit the ceiling.
Once everything is installed, drive a few drywall screws along the edge, where you can determine where the bolts are located.
Use about 7 first-
There are 10 screws along the height of the wall.
Now align the laser line with the bolt mark on the floor to do the job.
The laser line should show the exact center of the bolts behind the dry wall panel, eliminating any speculation.
Continue this way until all your walls are covered.
In order to protect the outer corner from damage, there is a metal corner on the dry wall.
If something hits the corner, the metal stand will take most of the impact and usually not cause much damage.
The bare drywall corners can even be damaged by a slight impact of something hard.
To connect the corner brace, first cut it into the right size using metal scissors.
It should fit from ceiling to floor.
Press the bracket on the corner with one hand (
Or have an assistant holding it)
, And use the dry wall nail to nail it in place.
Support should be as flush as possible with both sides of the wall.
Drive the nails every once in a while and make sure not to hit the damaged drywall or bracket with the wrong hammer.
Some people hate the job, but it's not bad.
Drywall tape is used to bridge the gap between adjacent pieces of drywall, so there is something to stick to the drywall compound.
Otherwise it will sink into the gap and you have to check it six times.
Drywall adhesive tape should be applied anywhere the two drywall edges meet, whether in a flat part of the wall and ceiling or in the inner corner.
The corner outside is not necessary because the angle brackets perform double
Duties in this regard.
It is important to be clean.
There should be no wrinkles or wrinkles on the tape and should be as straight as possible.
For corners, try pre-
Fold the tape before putting it in place.
Push the tape into the corner with a putty knife to get a nice, sharp angle.
Durabond is a high-end brand
The strength of the dry wall repair material is very beautiful.
It is very hard and strong when it dries.
Try to avoid using too much when you use it, because you will spend a lifetime grinding it off.
In this case, it will be used for the outer corners to increase the strength and for filling any gaps that the drywall compound cannot handle individually.
Mixed DURABONDDurabond comes for sale in powder form, so you have to mix it with water yourself.
"90" in the name means the drying time-90 minutes.
In the bathtub you don't mind throwing away, mix Durabond with tap water according to the instructions on the box.
The result should be a smooth gray paste that sticks to the wall without running.
Apply Durabond with a tro knife or a wide putty knife, apply Durabond paste along the corner brace, completely covering the metal.
Through a long, uniform stroke, skim along the surface to achieve a smooth finish without bumps.
If the scraping is too deep to reveal the edge of the nail head or bracket, please re-apply some Durabond and try again.
Scrape the excess back into the tub unless it is contaminated with debris.
Do both sides of the corner this way and work quickly before Durabond dries.
The process is a bit of a learning curve, so it never starts where it's too compelling, if possible.
To fix the larger gap, use the smaller putty knife to push Durabond into the gap.
Then, with a wider putty knife or spatula, skim along the length of the gap to make it smooth.
Make sure the filled area is not higher than the surface of the drywall, otherwise you will take a long time to fix it.
Clean up your tools as soon as they are finished.
Durabond sticks to the metal and destroys the fine edges needed to achieve a smooth finish.
Wipe the tool with a clean rag and wash off any residue in the water.
The process of applying a dry wall compound is often called smearing or skimming.
The basic idea is to apply one or more layers of drywall compounds (mud)
Hiding flaws on the wall
The most noteworthy is the gap and the screw head.
Between each layer, gently polish the dry "mud" to maintain a smooth finish.
Preparation of drywall composite drywall compounds is usually before sale
Mix in the big tub.
Try to get "dust control" if you can, which makes it easier to clean up later.
Just open the tub and mix it with a clean mixing stick and you can go!
Applying the first layer, you may have noticed that the edges of the dry wall panel are slightly tilted.
This is done so that the drywall compound can cover the gap and drywall tape without creating a raised vertical stripe.
Starting with a narrower spatula, the 6 inch is perfect.
Just tilt on the mud and lean it against the wall as you go.
When the entire length of the gap is covered, skip it again to make everything smooth and even.
Again, it takes a bit of practice to get it right, but I'm sure you'll understand it soon.
To cover the screw head, use a small 3 "putty knife and just skip it in the dimples area.
It takes very little mud to do this, and you can usually make five or six screws with a spoonful of mud.
When you're done, clean up any excess mud before the walls or floors dry.
Be sure to wash off your tools.
The mud doesn't stick to the tool like Durabond, but it's definitely easier to clean up when it's wet.
The mud in the corner is tricky.
I like to cover a thick layer of mud around the corner with a 3 "putty knife, and then pass over it with a wide-angle spatula to get a smooth surface.
This is probably the hardest part of skimming and it will take you a while to correct it.
Again, I would suggest starting with a dark corner first and moving to a more visible place when you have more confidence in your skills.
Obviously, you apply Durabond to the outside corner, covering the metal corner support.
Once Durabond is completely dry, you can skim it with mud to get a smooth surface.
Use a wide spatula covered from the corner, far above the edge of the Durabond layer.
When the dry wall compound is dry, polish the first layer and it changes from light gray to white.
It will be hard to touch and will feel warmer than wet compounds.
Usually it takes hours to a full day, depending on the temperature, humidity and air flow in the room.
The first layer can be polished using a more positive sanding pad (100 grit)
, Installed on a sponge scrub pad.
It doesn't take a lot of pressure, so relax.
All you need to do is eliminate the most serious violations.
My father-in-law likes to do the job with a pole sander, but I prefer to have close contact and do it manually.
Use your hand to feel the feeling of bumping.
In the corners, special sand blocks with grinding edges are used, and the grinding edges meet at 90 degrees.
When you are done, the room will be filled with dust clouds and almost every inch of you will be covered with a thin layer of dust.
When the dust settles, sweep as much as possible with a broom and then vacuum the rest.
Skip the second layer and the second layer of mud is like the first, although you will cover a wider area.
Use the 10 "spatula, not the 6" spatula used for the first skim.
As before, slide on some mud to make it smooth.
This may be the last layer you have to do if you work carefully.
Some screws may also require a second layer of mud.
Use the same 3 "putty knife as before.
Polish the second layer of the layer and switch to a higher sandpaper such as 150 or 180.
This will make the completion more smooth.
Carefully sprinkle sand everywhere and make sure not to remove too much material.
Pay special attention to incorporating the edges of the mud into the walls for a good smooth transition.
For better mixing, use a long scan action.
After finishing the polishing, continue to clean yourself and the room.
Hopefully you'll only have to do two SKUs, but maybe three in some areas.
It should not exceed that, though.
Most people have painted a little before.
The biggest challenge here is to prevent paint from flowing to places you don't want.
Go get dozens of color cards.
When you decide a color (or colours! )
Come back. let's review the basics.
Tool brush-
Small and medium should be enough. Paint Roller -
Make it easier to paint a large area
Use with paint piping tool-
For precise lines in the corner, do not have to use masking tapedlot paper-
Optional, only required if the floor is already installed. Material-
You need a primer and a top in the color of your choice. Masking tape -
It is a good idea to cover up small details from the ceiling, as any small drops of water that fall on the wall will be painted.
Before you start painting, it's best to brush off any dry wall dust left on the dry wall with a broom or rag.
Make sure you have enough light in the room you are working on.
If you haven't connected the lights yet, use a portable work light or work during the day.
Clear everything on the floor as water drops may appear.
Unless you have already installed the floor, there is no need to cover the floor with dropped sheets.
PRIMERThe primer has two functions, it helps to seal the drywall and provides the base color for the finish paint to match the color on the sample.
It can also cover pencil marks and other flaws so they don't show up.
You can use a white primer, but usually you can use a primer of one or two colors lighter than a finish coat.
Brush in use, draw in all corners and anywhere you can't reach with paint rollers --
Lights, vents, etc.
You can work directly from the paint can if you wish.
After completing the small sections and corners, you can start using the rollers.
Set the roller tray in the middle of the room and fill the bottom of the tray with paint.
Dip the roller into the paint and use it to apply a little paint on the ridge part of the tray.
Then, roll the whole surface of the roller in the paint.
Roll the paint roller along the ceiling and paint in 4 feet sections.
Repeat and continue when the paint on the roller runs out.
After checking the primer to dry, check if there are visible flaws on the surface of the drywall.
Usually, a uniform layer of paint on the surface will help to reveal the bumps, dents, and other defects that were not previously visible.
If you notice any defects in your skimming, simply break the dry wall compound and pat it on the primer.
After drying, paint the part you repaired with a primer.
The TOPCOATThe method here is the same as the primer, just with a different paint.
Take special care of your craft this time.
Make sure there are no missing spots on the whole surface and no lighter areas with less paint.
When the paint is still wet, it's easier to correct the problem now, instead of checking them with a small brush a month later when your wife points out the problem.
The process here is the same as the ceiling, but there is one
How do you avoid accidentally applying paint to the ceiling?
In the absence of any additional tools, painters who are not professional in cutting will do so
With a high quality brush, simply draw a precise straight line along the inner corner, the edge of the brush is in the corner, but never touches the ceiling.
It sounds simple, but when you work on top of your head, your arms get tired quickly.
On higher ceilings, it's hard to reach the height and precision you need.
Fortunately, there is a tool to help you.
It's basically a long, flat piece of metal or plastic that you can push into the corner and paint.
Like moving tape.
You may not need much masking tape when painting.
However, it may be useful in narrow areas where larger tools do not fit.
However, it would be great if you were going to paint stripes and other patterns on the wall.
When using masking tape, make sure the surface is clean and dry.
Press hard, especially on the edges, so that the paint can not be sucked dry below.
Also keep in mind that the "working life" of masking tape usually printed on the package is limited.
The painter's tape usually has 7-
Depending on how much you want to spend, 14 days-
So, after sticking to it, make sure you get any work done quickly.
Avoid not painting sockets, switches and fixtures for sockets and switches. That is all.
The door frame needs to be strong to support the weight of the door and the force to open and close (
Open the bang? ).
We will add extra bolts on both sides and top of the door.
There are many different widths for measuring rough open doors, the standard is 32 ".
When you bought a pre-
Hanging doors, providing measurements for the "rough opening" required for door installation.
The rough opening is slightly larger than the door frame on all sides, so you can insert the gasket to align the door frame precisely so that it can be opened and closed smo