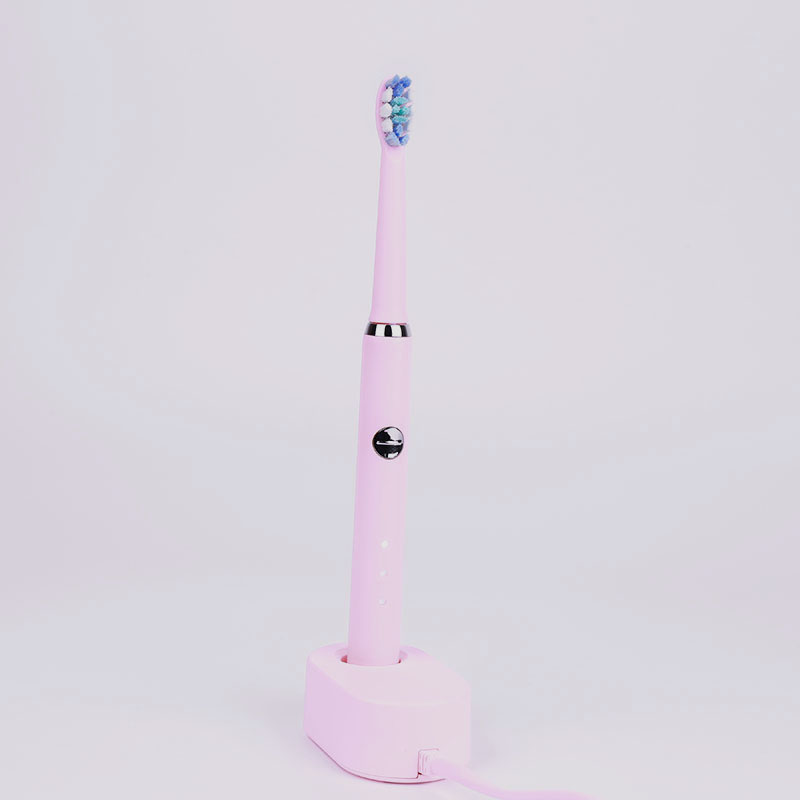
This desktop air purifier/welding fan is a great project-
It integrates some electronic products, carpentry and general repair and repair.
Not to mention it's a great table accessory, perfect for removing any smell in the air or for use when welding.
The device is small and lightweight, and you can carry it with you.
Put it on the desk in the office, in the car, or wherever a little fresh air is needed!
Not to mention, if you turn the air purifier on, then you have your own desktop fan, which is really cool.
Parts: Method: Let's start with basic parts.
I have two 90mm 24 volt computer fans and I bought mine very cheaply from the used sale at the local university, but you can order it online at any time.
I am using a 12 v dc power supply but since they are 24 v fans I would like to be able to take advantage of the extra capacity and I am going to connect them to the voltage booster
To control the speed of the 24 volt fan, you need a voltage booster.
About voltage boost de-
Weld the potentiometer with a 10 k Ohm potentiometer/switch and extend the line, adding two 3 k ohm resistors at the same time.
Weld the input negative power cord in parallel with the voltage booster to the switch and fan.
Set the maximum voltage by adjusting the potentiometer and range on the boost by the 10 k Ohm switch.
Confirm the expected value with a multimeter.
If you want to avoid the booster and extra work then you can connect the fan directly to the 12 V power supply and use the switch.
So now, to put it simply, wrap all these parts in a neat little package.
I decided to make the box with the medium fiber board, here you can see that I am using Xcarve, which is a CNC machine to cut the parts.
I have an svg file that I can use if others want to do the same.
Of course, if you don't have X-
Carving, then you can cut the pieces off with a saw, I have a set of templates that you can print out, stick to the pieces and get all the holes done.
In this case, I prefer to stick to the paper with glue and then cut the holes with a drill or bit.
For two big holes, I use a 3-inch 1/4 hole saw.
Once you cut all the parts of the box, it's time to connect them.
I prefer to apply some yellow glue on the edges and some hot glue.
When the yellow glue is set and dry, the hot glue works like a clip.
I put a few small supports in the corner to provide a little extra power.
Now, as a filter, I ordered a charcoal filter for the range fan.
I just put it in the box and then I dig out the space for the little support in the corner.
I also doubled with two filters and went ahead and put the boxes together.
I also glue some of the thicker support pieces together and I will glue these to the box where the backing is screwed in.
OK, now that I have finished the basic box, it means that all the edges are together except for the box with fan holes at the back, and these holes will be screwed in later.
Finally, I start with the shellac coating and then polish it.
Then a primer.
I also add spackle in any defect.
The pieces are then painted white with flat paint and decorated with water-based polyurethane.
So the box is done and now let's go back to the contents of the box.
Here I will trim some wires and weld some of them in place.
Here we have a power supply connected to the switch part of the potentiometer.
I am inserting the filter into the box.
I have these slim mid-slim boards I cut to keep the filters in place in the box and I just stick them to the support to keep everything clean and tight.
Next, I screw the fan to the back and the hole fits perfectly.
To clean up some of the wires, I wrapped them together so they would stay together and tie them to the fan with a plastic zipper just because I don't want the wires to be everywhere.
It's time to connect everything.
So I connected the wire I screwed off the fan to the booster and fixed it in place.
At different stages I confirm that everything is OK and nothing is short or loose.
Then I bring the part into the box, especially the potentiometer twist knob that is placed on the side of the box.
I put a nut outside and fixed it down.
The power cord is at the back, right under the fan, perfect.
I then stick hot around it to make sure it's in place.
Also fix the booster to the side of the box with some hot glue and some wires as I don't want them to interfere with the fan.
Then it's time to turn off the back and install the fan in, I screw the back in place with some small screws that will insert into the support I stick together.
OK, now to make the knob on the side a little more comfortable to turn, I decided to make a bigger knob.
There is a walnut on the lathe.
Then I just drill a hole in it so it can be placed around the metal knob.
I am fixing the big knob on the small knob with epoxy.
Well, now we are ready.
This is a very interesting project and it works very well whether you use it to clean the air, Weld or personal fan.
To get a better perspective and download svg & PDF files, make sure to check the video.