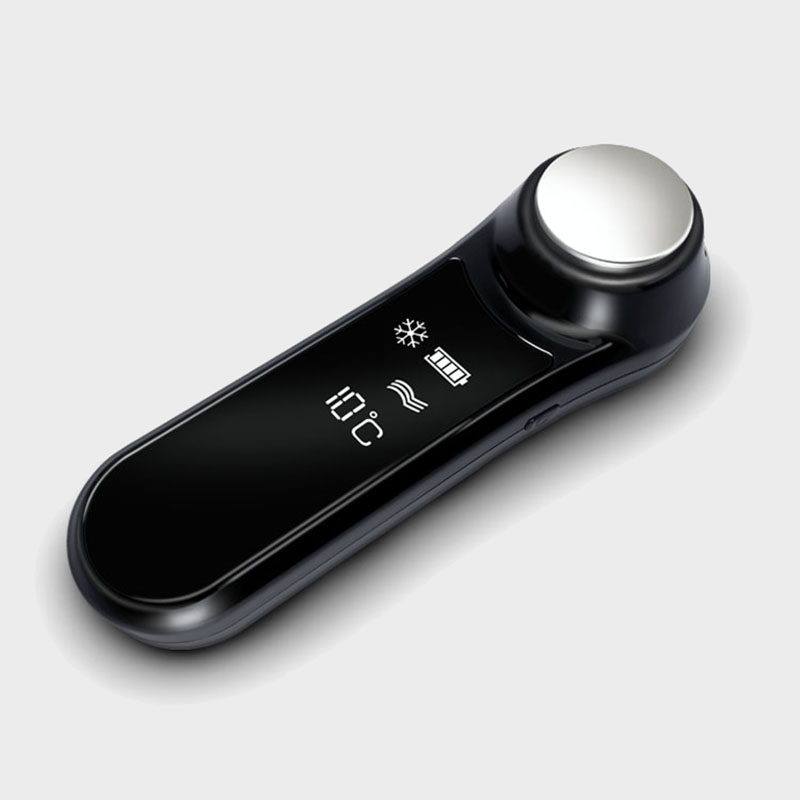
If you are conducting tissue culture experiments, it is essential that a tissue culture hood is now commonly referred to as a biosafety cabinet.
This structure describes the way I made it myself (first picture).
Just wanted you to know how these biosecurity cabinets work.
The second picture describes the way to create a sterile environment in a cabinet.
Air is cycled through an efficient air filter to filter out particles such as bacteria and most viruses.
The cleaned sterile air flows from the top, then through a slot in front of the cabinet and a slot in the back of the cabinet, up through a hollow cavity in the back than pushing the non-Blower
Repeat through sterile air and circulation of the filter.
Some air enters the atmosphere through smaller filters, and some air enters the cabinet from the front opening.
These cabinets are expensive.
The new price is almost $10,000, and the old price is about $2,000.
A bigger problem is that these problems are huge and heavy.
It is difficult to adapt to small laboratories.
So, I think I can try to do it myself.
The trick is to use the existing HEPA filtration unit found in the large room air purifier unit.
The final result is good.
This version of the youtube summary can be found here.
I decided to design by a) off standard
Pushing the air through the filter instead of pushing the filter will reduce the turbulence on the filter, B)
There is a regular mesh of holes at the bottom so that the air flow is more uniform
Reduce turbulence again.
I also decided to use lightweight materials such as wood and plastic so I didn't need a forklift to move it.
The second picture is the overall structure of the cabinet skeleton.
The unit is 36 inch wide and is about the same in height.
The depth is 28 inch.
Wooden strips (2.
5 inch wide, 3/4 thick)
First used to form the bottom and back.
Glue and screws are used to make the base as shown in figure 3rd.
The strip is covered with recycled 1/4-inch plywood.
I then glued the small Pergo floor to the primer strips to support the vertical strips.
The back is made by sticking 4 vertical strips to the Pergo floor.
After the glue was dry, I stuck a piece of cardboard to the back.
The strip is temporarily fixed in the appropriate position to obtain the actual size of the part that makes the edge.
The front is tilted 10 degrees from the vertical direction.
I then cut two sets of the same strips for both sides and stick them to the existing blocks and screw them together.
I then cut two panels from the scrap cardboard and glued them to the outside of the strip, creating two sides for the Cabinet.
The reason I have confidence in the Cabinet using wood instead of metal or plastic is that I know that by coating all exposed surfaces with a polymer used to seal the flat roof, I can make all exposed surfaces that are not affected by the water.
I have a few barrels of SureCoat material left over from my DIY homework for roof repair, which I have done before.
I first roll a layer of gel like SureCoat on all surfaces, then apply a layer of polyester mesh on the edge of the cabinet, and apply another layer of SureCoat on this mesh.
The adhesion of SureCoat is very high and dry into a hard surface as the design air enters the bottom of the cabinet and moves up through the back and sides of the cabinet.
I forgot to provide air access to the side of the cabinet, so cut some grooves for air access to the side of the hollow cabinet.
I had to repaint these surfaces with SureCoat because of the newly exposed wood.
The cabinets began to take shape.
For the inside back panel, I decided to use the very hard Pergo floor panel I got from freecycler.
I cut them into size and then test them later to see if they fit.
On the bottom panel, I added a slot for the AC GFC socket (bought new)
Power switch and socket.
The power switch and plastic panel that will cover the opening are also from freecycler.
This AC socket will provide power for materials such as Pipet Aids used in the tissue culture hood.
I connected the socket as shown in the figure.
Strong mains lines were used.
Bare copper wire goes to the "Earth" hole on the AC socket and then wraps around the Earth screw on the switch.
The black charged wire leads to one end of the switch.
A black wire connects the output of the switch to the AC socket.
White wire (Neutral)
Went directly to the AC socket.
The socket is connected to the back panel with a foam insert to prevent air from leaking through the entire socket assembly.
The rear panel is installed in the cabinet, followed by a test fit for the bottom perforated panel.
The bottom panel is the polypropylene peg board I bought online.
In order to measure and connect to the side wood strips, two internal side plates were cut.
I have run out of white strips long enough.
5 inch bare wooden strips to create a frame to accommodate the HEPA filter assembly.
Four connections to each other (
Glue and screw docking)
Create a rectangle about 10 inch from the top of the cabinet.
The rectangular frame is then connected with screws to the side and back of the cabinet.
The HEPA filter will stay on a rectangular frame.
The entire air moving assembly consists of two main parts-
The actual HEPA filter has the plus and attached fan groups set up, which will increase the required air flow.
Hopefully the first chart will explain this.
I have a room air purifier from RabbitAir and we haven't used it for more than three years, so even though I will recycle it for tissue culture hood.
The device has four levels of air purification-
Pre-filters that can block hair and lint, and HEPA filters that can block 99.
0 particles 97%.
3um or larger size, activated carbon filter, and finally air ion generator.
More importantly, it is easy to provide a replacement filter at a lower cost (about $50)
Commercial Tissue culture Hood filters that cost about $500 or more.
Figure 3rd is the Congress of this HEPA established.
I am planning to add more details about unplugging the air purifier in the youtube video.
The back of the air purifier is the body cloth of the blower.
This back is fixed on a piece of cardboard with screws.
The air at the outlet will be guided by a guide plate made of triangular plywood and a lid to form a pipe.
The image shows the steps to create this pipeline.
Blower motor units and associated circuit boards are installed in a gray base.
The frame to hold the filter is trimmed into extra plastic and then connected to the base with the original screw.
The filter is then placed within the frame.
I created a layer of fans (
From freecyler again)
Help to increase the airflow if needed, and even the airflow.
This 110 V fan comes from freecycler that I connect to a perforated hard board.
After cutting the holes for the fan and covering the performance board with a grid, the fan is connected with a double-sided foam tape.
The fan is connected in parallel.
Connect the wire on the fan through a hole on the HEPA panel (second image).
The panel with the fan is fixed to the bottom of the rectangular wooden frame, while the HEPA panel is placed on the top of the rectangular wooden frame. The top-
The front panel is made of Pergo floor and connected to the cabinet with screws.
The top panel is cut off from the hard board.
I didn't have 36 inch before 18-
There are two tempered glass panels of 18 inch square meters. I used these.
They are supported by aluminum L-
Screw into the channel on the side of the cabinet.
I can add hinges on these panels or convert the settings to a sliding panel.
Not yet decided.
I slide the perforated polypropylene sheet into the bottom.
This bottom plate is removable for easy cleaning.
An iec ac In socket is added to the bottom of the cabinet on the back panel.
The wire is guided through the hollow back to the top.
The wire is connected through the terminal.
The wiring diagram shows the main wiring from the IEC socket
The ground wire is connected to the ground wire of the cabinet-AC-
Socket connected to the rear panel.
The neutral wire is directly connected to the HEPA unit, fan and cabinet from the IEC in the socket-AC-
Socket and cabinet light and UV light.
The live wire of IEC in the socket is first connected to the fuse holder.
The other end of the fuse is connected to the power switch.
The output of the power switch is connected to one end of the three switches.
The other end of these three switches is connected to: the charged end of the auxiliary fan, the Cabinet light wire and the UV light wire.
The live output of the power switch is also connected to the live wire of the HEPA filter and cabinetAC-socket.
There is a rectangular hole on the front panel to fix the LCD panel on the air purifier.
The PCB is then attached to the baffle that fits the hole.
The original dust sensor of the air purifier is attached to the interior of the chamber at the top of the tissue culture Cabinet.
I have been testing the airflow with a digital anemometer until the later stages of construction, which helps to optimize the position of the fan and hole to guide the air.
I have taken the video footage and I still need to edit it to the youtube video.
This shows the removal of the RabbitAir air purifier, as well as the Cabinet test with air flow meter, and of course the operation of the unit.
Hope to receive these in a few days and attach the link to this structure.
I also have to do particle retention testing and aseptic functional testing, but these are more of the properties of the HEPA filter --
Yes, I should order a brand new set. The lights (
LED light and UV light)
Still to add
I do have UV fluorescent lamps, but I have to convert the CFL electronics to run these UV tubes.