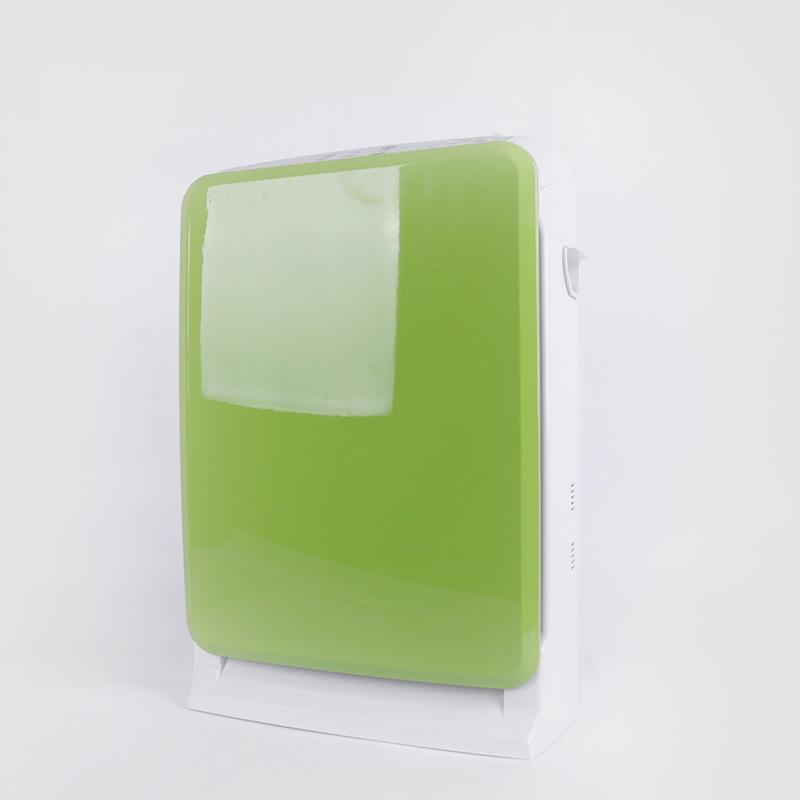
Research overview of the need to improve indoor air quality (IAQ)
A gas phase filtration device capable of removing pollutants such as volatile organic compounds (VOCs)
Tobacco smoke, carbon monoxide and formaldehyde.
Strategies to remove these harmful contaminants include the use of packaging
Bed or absorbent-
Closed filtration media such as microfibre adsorption agent
Supported Media (MSSM). Through a wet-
Sintering of Laidprocess, MSSM-
Micron-level locking matrix
The size of the fiber can wrap up the absorbent particles as low as 30 microns in diameter, thus having better chemical removal efficiency and higher adsorption utilization rate than the traditional filling bed.
Disadvantages of the adsorption agent-
The closed medium is a high pressure drop generated by a small closed absorbent particle, and the saturation capacity is low due to the relatively thin thickness of the medium (Harris et al. 2001).
In order to maximize the utilization of the adsorbent, a new strategy for the construction of a more efficient gas phase filter needs to be studiedentrappedmedia. Pleated and V-
Bank filters are two designs that can improve the pressure drop performance and overall capacity of filtration devices made of these materials.
By understanding the pressure drop limits in these filtration systems, additional media and adsorption materials can be packaged into one unit to improve pollutant removal capacity while maintaining acceptable resistance.
The following article, the first part, discusses the creation and use of a model that can predict the initial flow resistance in a folding filter with a depth of 89mm (3. 5 in. )or less.
The second part of the article will extend the model described below to the bugdev-
A bank consisting of multiple folding filters.
The flow resistance of the background filter is a key design and operational parameter.
The large pressure drop on the filter will overload the air handling unit and reduce the airflow.
More importantly, the pressure drop is directly related to the energy consumption of the filtration system.
Energy consumption accounts for 80% of total costs, while labor and procurement costs account for 20% of the remaining (Arnold et al. 2005).
There are many filter designs on the market, but folding filters are one of the more popular styles due to their unique performance advantages.
The folding filter uses a highly folded medium to increase the filter area available and extend the service life of the filter.
The additional area also gives additional advantages to reduce filter pressure drop and energy consumption.
The resistance on the folding filter conforms to the geometry ([K. sub. G][V. sub. f. sup. 2])and media([K. sub. M][V. sub. M])term. [DELTA]P = [K. sub. G][V. sub. F. sup. 2]+ [K. sub. M][V. sub. M](1)
Experience and computational fluid dynamics (CFD)
Chen and others have tried some methods. (1996)
River and Murphy (2000)
, Caesarand Schroth (2002)
Del fablow, et al. (2002)
Tronville and Sarah (2003)
Determine the constant.
Although accurate results are produced by each method, due to heavy reliance on empirical data, these models are only applicable to specific filters studied and lack predictive power.
Contribution of the fold tip and filter housing mentioned by Raber (1982)
, Is often ignored in the model.
The research objective is to develop an accurate model that, as an analytical design tool, can predict the initial pressure drop performance of the Fold filter unit based only on the thickness and permeability of the medium used.
The geometry of the filter and the effect of the packaging are quantified in a way that can be generally applied to various wrinkle filter designs with a depth of less than 89mm (3. 5 in. ).
The model consists entirely of algebraic equations for rapid optimization and predictive calculation to improve practicality.
The method used to build the model is similar to idelchik's (1994)
Method used to calculate the voltage drop of electrostatic filter.
In this method, the total voltage drop of the afilter is modeled as the sum of the smaller component resistors.
The individual components of the folding filter are derived from the assumed airflow path introduced by Raber (1982).
Then, by using Forchheimer-to work out the effect of each component on total filtration resistance
The Darcy's law, the bonuli equation and the continuity equation are extended.
Due to the interaction between components of the pleat filter, the modeling method cannot simply analyze and quantify the precise pressure drop impact of each component.
Therefore, the model is an empirical determination of the relative impact on each term in the presence of all other terms.
This is achieved by systematically changing the design variables, systematically evaluating the net increase in total filtration resistance, and then contributing this effect to the appropriate variation item.
Fochheimer theory
The Darcy's law in the granular air filter is extended, with high operating speed (
Renault number> 20)
It usually leads to a nonlinear departure from Darcy's law through the flow of media (
River and Murphy 2000Chen et al. 1996).
Rivers and Murphy conclude that the biased penetration medium is a product of fiber compression because the inertia of the air compresses the fibers of the medium together at a higher operating speed.
Compression changes the internal void volume and twists and turns of the medium, resulting in an increase in surface speed, a decrease in permeability, and a non-linear increase in total resistance.
A practical way to explain the behavior of non-DASIA is to add a second-
Order Conditions of Darcy's law (
Scheideger 1974).
Equation 2 is called Forchheimer-
Expanded Darcy's law.
A is equivalent to the constant of Darcy's law ([mu]L/[kappa]).
B explains the nonlinear deviation caused by the inertia effect. [DELTA]P = A[V. sub. M]+ B[V. sub. M. sup. 2](2)
There are various theoretical equations that try to relate to the physical meaning of the second medium constant, but these theories require a broad understanding of the fiber size and stacking density of the medium (
River and Murphy 2000.
The research presented by Rivers and Murphy shows that it is complex and difficult to accurately model media performance with these theories.
Since the main purpose of the study is to identify and determine the consistency created by geometric design parameters rather than media, it is better to use a quick modeling of media constants without introducing so many empirical methods of theoretical errors.
The Buruli equation mechanical energy balance is the sum of kinetic energy, potential, mechanical, compression and viscous energy terms (Bird et al. 2001).
The bonuli equation is assumed to be uncompressed, stable-
The state flow when controlling the volume is maintained with a stationary solid boundary.
By eliminating the elevation changes within the control volume, operating under turbulent conditions, and removing all mechanical work, the ranking of berulife can be further simplified.
When used between two points, the following equation results :[DELTA]P = [P. sub. 1]-[P. sub. 2]= [1/2][rho]([V. sub. 2. sup. 2]-[V. sub. 1. sup. 2])+ L[upsilon](3)L[upsilon]= [1/2][rho]K[V. sub. i. sup. 2](4)
The viscous loss term Lv explains the change in mechanical energy converted into heat due to the viscous force (Bird et al. 2001).
It is determined by solving mechanical energy and momentum balance at the same time or by experimental measurements.
As a coefficient of friction, the K value is a function of the geometry, Reynolds number, or both.
The V term is the reference speed based on the coefficient.
This reference speed is optional at will, but it must be the inlet or outlet speed that enters the control volume.
Previously, K values have been calculated for flow systems such as sudden shrinkage [K. sub. C]
Suddenly expanding [K. sub. E]
And through the perforated plate [K. sub. G](Idelchik1994). [K. sub. C]= 0. 5 x [([1 -[A. sub. Free]]/[A. sub. Total]). sup. 0. 75](5)[K. sub. E]= [([1 -[A. sub. Free]]/[A. sub. Total]). sup. 2](6)[K. sub. G]= [([1. 707 -[A. sub. Free]]/[A. sub. Total])[([A. sub. Free]/[A. sub. Total]). sup. -2](7)
Flow pattern in folding filter air through seven different cross areas
Section flow area of pleat filter (Figure 1).
It is assumed that a uniform flow profile exists in the upstream pipeline before the filter.
A typical fold filter uses a grating to increase the structural integrity of the filter and fold.
The flow is contracted through the grille, resulting in an increase in speed.
The air expands back after the grille, but when it is directed to the tip of the folds and around the folds, it quickly shrinks for a second time. [
Figure 1 slightly]
Once entering the folds of the filter, the airflow begins to split and change the direction to allow access to the medium at an angle perpendicular to the surface of the medium.
After the direction changes, the Air expands to the surface area of the media.
The proposed flow pattern through filter folds is very similar to the flow of convergence or divergence.
The fourth area is the surface area accessible to the media.
The area does not include a small portion of the media that will be closed in the pletips.
After flowing through the medium, the airflow goes back to the downstream pipeline along the same but opposite path as the filtration system.
The general schematic diagram of parameter recognition is given.
This term can be found at the end of the paper.
The pressure drop assessment of the flow system by folding the total pressure drop of the filter will be modeled as the sum of the individual resistance.
By applying the bonuli equation or forchheimer-
Extend Darcy's law to the seven flow regions proposed above.
The result is a system of equations as follows: * through the front grating :[DELTA][P. sub. 1]=[1/2][rho][([V. sub. 2. sup. 2]-[V. sub. 1. sup. 2])+[K. sub. G][V. sub. 1. sup. 2]]
* Flow from grille to pleats :[DELTA][P. sub. 2]=[1/2][rho][([V. sub. 3. sup. 2]-[V. sub. 2. sup. 2])+[K. sub. C][V. sub. 3. sup. 2]]
* Flow from the entrance of pleat to the surface of the medium :[DELTA][P. sub. 3]=[1/2][rho][([V. sub. 4. sup. 2]-[V. sub. 3. sup. 2])+[K. sub. P1][V. sub. 3. sup. 2]]
* Media traffic :[DELTA][P. sub. 4]= [AV. sub. 4]+[BV. sub. 4. sup. 2]
* Flow from the surface of the medium to the exit of pleat :[DELTA][P. sub. 5]=[1/2][rho][([V. sub. 5. sup. 2]-[V. sub. 4. sup. 2])+[K. sub. P2][V. sub. 5. sup. 2]]
* Extended to raster from pleat socket :[DELTA][P. sub. 6]=[1/2][rho][([V. sub. 6. sup. 2]-[V. sub. 5. sup. 2])+[K. sub. E][V. sub. 5. sup. 2]]
* Grille on the back :[DELTA][P. sub. 7]=[1/2][rho][([V. sub. 7. sup. 2]-[V. sub. 6. sup. 2])+[K. sub. G][V. sub. 7. sup. 2]][DELTA][P. sub. F]= [SIGMA][DELTA][P. sub. i]= [DELTA][P. sub. 1]+[DELTA][P. sub. 2]+ [DELTA][P. sub. 3]+ [DELTA][P. sub. 4]+[DELTA][P. sub. 5]+ [DELTA][P. sub. 6]+ [DELTA][P. sub. 7](8)[K. sub. C], [K. sub. E], and [K. sub. G]
Friction coefficients were previously calculated by equations 5, 6 and 7. [K. sub. P1]and [K. sub. P2]
It is the friction coefficient of the flow in the upstream and downstream folds.
By solving mechanical energy balance and momentum balance at the same time, a new coefficient formula can be determined.
Figure 2 is the fold control volume used to address the balance of the downstream fold coefficient. [
Figure 2:
Momentum balance]d[GAMMA]/dt]= [[V. sub. 1][W. sub. 1]+ [P. sub. 1][A. sub. 1]][U. sub. i]-[[V. sub. 2][W. sub. 2]+ [P. sub. 2][A. sub. 2]][U. sub. i]+ [F. sub. s[rightarrow]f]
Mg force of fluid to y-inherent strength
Therefore, it is suitable to be installed at the back of the filter without interfering with the pressure measurement.
There is a window at the top of the filter box to verify that the integrity of the folds remains the same during the experiment.
Monitor the pressure drop of the filter section through the Dwyer Mark II monometer and the anaconsys IPO10 differential pressure transmitter.
The equipment is connected 3mm upstream of the pipeline (1/10th in. )
Pressure 250mm (10 in. )
Before the filter test box.
The hotel's downstream connection is open to the atmosphere of the room.
The exit of the transmitter is located at 150mm (6in. )
Before the end of the export section.
The outlet partially prevents the increased pressure drop due to sudden expansion into the room.
National Institute of Standards and Technology
Calibrated Extech 451104vane-
The anemometer monitors the outlet speed and temperature of the test bench outlet.
Speed measurement by a 9-
The point grid program outlined in ASHRAE Standard 52. 2, Section 5. 2 (ASHRAE 2007).
The air from the blower is drawn from the room.
All the tests were carried out in about 20 [degrees]C (68[degrees]F)
Environment and altitude 215 (705 ft)
Above sea level;
Therefore, it is assumed that the constant density value of air is 1. 16 kg/[m. sup. 3](0. 0725 lb/[ft. sup. 3])
During the whole experiment
Collect the filter data by setting the inverter to the desired frequency and recording the corresponding values of the pressure sensor, pressure gauge, differential pressure transmitter and bladeanemometer.
Repeat the process at 15 evenly spaced data points between 5 to 40Hz. The 15-
A point test was copied for each filter.
After collecting the data of the filter, the pressure drop curve is created by drawing the relationship between the surface speed and the pressure drop.
Using the frequency and resistance on the blower, calculate the surface speed from the blower curve.
The value was verified by vane-
Anemometer measurement.
The pressure drop is measured by the pressure sensor and the cross sensor
Check by Force meter.
Each pressure drop curve fits a regression line for data analysis and elimination of individual data differences.
Small background resistance of the system by using Darcy-
Weisbacheation.
The purpose of the experimental procedure for determining model parameters is to verify the effectiveness of using previously published coefficients to model specific aspects of filter design, as well as to empirically determine new friction coefficients encountered in pleats.
Since the media constant will be unique and will vary with the medium used in the filter, this method begins with measuring the media constant (A and B)
Thickness of all materials used in the study.
Coefficient previously published [K. sub. G], [K. sub. C], and [K. sub. E]
It is then proved to be applicable.
The pleat coefficient of a single filter is determined according to experience [DELTA][P. sub. F]
Data with facevelocity.
This technique is based on the method of identifying constants N and [of rivers and murals]K. sub. G]
From their models.
A more general coefficient has been developed by determining [K. sub. P]
Multiple filter designs.
The media constant in Figure 5 shows the results of the resistance and surface velocity obtained from the plane Media sample.
Each point on the graph represents the data collected by the experiment.
Fitting line corresponding to article 2
Polynomial of order;
Therefore, the use of equation 2 is the first choice for linear Darcy's law.
Fitting constant and R-
Square values are given in Table 1. [
Figure 5 Slightly]
Friction coefficient of grating ([K. sub. G])
Hydraulic resistance manual (Idelchik 1994)
Use equation 7 to calculate the coefficient of friction when the fluid flows through the shape perforated plate.
In order to verify that the filter shell can be modeled with the same formula, the frame is modified and the corresponding measured pressure deviation is compared with the calculated deviation.
The filter for grating experiments consists of 2 Media, 22 pleats per filter, with a size of 491mm x 21mm (19. 5 in. x 19. 5 in. x 0. 85 in. ).
The normal housing of the filter consists of a diamond mesh blocking 34.
Flow area of 5% square meters.
Add extra grating evenly at the front of the filter to remove the blocked flow area from 34. 5% to 59. 4%.
Subsequently, the grating of the filter was removed with only 16 results.
The flow area of 0% is blocked.
For each grating configuration, the relationship between pressure drop and surface velocity is shown in figure 6.
Marking represents the observed data. the real line is Excel-
Fitting regression line. [
Figure 6 slightly]
Since the same filter is used in all three tests, the observed differential pressure between curves can be generated by grating modification only.
The low blocking filter curve can be used as a reference to quantify the additional resistance generated by extrusion.
The observed increase in flow resistance between normal clogging and low clogging filters is then compared to the expected pressure increase calculated using equation 4, which has a friction coefficient determined by Equation 7.
Below, calculate the friction coefficient of the following blocking profile using equation 7: for normal plugging :[K. sub. G]= [(1. 707 -0. 655)/[(0. 655). sup. -2]]= 2.
Low Block 50 :【K. sub. G]= [(1. 707 -0. 840)/[(0. 840). sup. -2]]=1.
High blockage :[K. sub. G]= [(1. 707 -0. 406)/[(0. 406). sup. -2]]=7.
89 This calculation is repeated for the difference between high blocking and low blocking filters.
The results of the measured and calculated differences are shown in Figure 7.
Due to the overlapping of calculated and observed differences, equation 4, which is combined with equation 7, can be used to adequately predict the pressure loss caused by the filter shell.
The grating on the back of the modified filter and the filter type S and T (see Table 2)
The experiment was carried out.
While it is observed that the grating resistance has nothing to do with volume and permeability in the parameter space explored, caution should be taken when applying these equations to low or higher permeability
Wrinkle systems such as Minipleat panels.
The unique design of this filter may cause the flow field around the grating to be affected by folds;
Therefore, the use of equation 7 will no longer be valid. [
Figure 7 Slightly]
The fold tip assumes that the shrinkage and expansion inside and outside the fold is assumed to be the coefficient of friction obtained using Equation 5 and Equation 6 is accurately modeled by equation 4.
For the calculation of friction coefficient ,[A. sub. Total]= [F. sub. W]x[F. sub. H]and [A. sub. Free]= ([F. sub. W]-[P. sub. C]x [P. sub. T])x [F. sub. H].
Without inadvertently affecting other resistors, it is very difficult to experimentally change the folds and analyze the contribution of the resulting resistors.
The assumption that Pleattip acts as a wall is based on Darcy's law.
When the medium is folded, the porous material is folded on its own top, creating folds of increased thickness and/or reduced permeability.
According to Darcy's law, both the increase in the thickness of the medium and the decrease in the permeability will lead to greater flow resistance.
Therefore, due to the increase in resistance, the airflow through the tip of the fold is considered blocked and will be directed around the tip of the fold.
This assumption was previously included in the study by Caesar and schross (2002)
And by Raber (1982).
Friction coefficient of folds ([K. sub. P])
Determine the fold coefficient of a specific filter by obtaining [DELTA][P. sub. F]
Face speed data relative to the speed range.
The model is rearranged into the following linear form :[DELTA][P. sub. F]-[1/2][rho][(2[K. sub. G])[V. sub. 1. sup. 2]+([K. sub. C]+ [K. sub. E])[V. sub. 3. sup. 2]]+ B[V. sub. 4]+ A[V. sub. 4. sup. 2]= [1/2][rho][K. sub. p][V. sub. 3. sup. 2](10)[V. sub. i]
Use the continuity equation to calculate the value from the surface velocity.
Coefficient [K. sub. G], [K. sub. C],[K. sub. E]
List A and B with the methods discussed earlier.
By subtracting these known flow resistance from the total pressure drop measured by the experiment, the friction coefficient of the filter is empirically determined.
Then the difference will be compared with the reference speed term ([1/2][rho][V. sub. 3. sup. 2])
, And infer the fold coefficient from the slope.
Figure 8 shows 491mm x 21mm graphically (19. 5 in. x 19. 5 in. x 0. 85in. )
1 media filter with 42 pleats.
The real line is the least-
Square regression fitted with the pressure drop data measured by the experiment.
The dotted line is a model compilation of known flow resistance, which is due to the flow through the media, the blockage generated by the filter grating, and the channel due to the contraction and expansion of the tip.
Hyphen represents the smallest observed-
Square regression and model line, which is equivalent to the left-
The hand side of equation 10.
As shown in seoer figure 8B, the observed differences are drawn ([1/2][rho][V. sub. 3. sup. 2])for the filter.
The slope of this line is equal to the fold friction coefficient. [
Figure 8:
The resulting coefficient is only valid for filters with the same geometry.
In order to obtain a more general coefficient of the model, it is necessary to determine the fold coefficient for a large number of fold counts, filter depth, medium thickness and intermediate capacity.
20 filter variants manufactured by qualityfilter, Inc.
In robersdale, Alabama, it is used to determine the fold coefficient.
The fold coefficient of each filter is determined by the same method described above.
Filter, geometric parameters, type of medium, fold coefficient observed and R-
Square fitare is given in Table 2.
The formula for the friction coefficient of the fold should be based on the Reynolds number, the non-dimensional geometric ratio, or both.
The Reynolds number has a significant effect on the coefficient only when there is a flow, but for the test conditions encountered, the flow is almost always turbulent.
Therefore, the Kp coefficient depends only on the geometry.
The partial decomposition of momentum and internal energy balance shows that the fold coefficient should be related to the function [([P. sub. L]/[P. sub. O]). sup. 2].
Figure 9 shows each experiment
The coefficient of determination with the function.
It is obvious that this function has no direct correlation with the observed coefficients.
Since the assumptions made to solve the mechanical and momentum balance at the same time are simplified, this can be expected.
A general power law trend is visualized between functions and pleat coefficients.
However, the dotted line is a power law function with a general formula
The square value dropped to 0. 87.
It is particularly noteworthy that the filter with the largest wrinkle tip blockage (
Type P, R, and S)
Have a higherthan-
The mean coefficient indicates that the additional resistance effect is absorbed into the pleat coefficient.
This supports the use of separate terms for pleat prompts.
Discussion Figure 11 shows a model that compares the calculated values of all 600 observed pressure drop data points compiled from 20 different filter types. A least-
Square regression line showsa one-to-
A letter
The dotted line indicates [+ or -]
5% from the regression line. [
Figure 11 omitted]
Fold the "U" curve due to tradeoff of media-
Induced pressure loss of stickiness
Induced pressure loss, the folding filter will experience the minimum pressure drop corresponding to the optimal number of pleats.
Preliminary research by Chen et al. (1996)
Del fablow, et al. (2002)
, Tronville andSala (2003)
Caesar and schrose (2002)
Each gives a graph of pressure drop and fold count that shows this "U" fold curve. Chen et al. (1996)
Mark the bottom pleat count on the left side of the best number as media-
Ruling regime.
The picture is said to be in viscosity-
When the filter has more than the optimal number of folds, the dominant regime. [
Figure 10 slightly]
The traditional pleat "U" curve bymodeling generates a 491x21mm (19. 5 x 19. 5 x 0. 85 in. )
Filter with FM1media constant and thickness.
Figure 12 is calculated by keeping the velocity constant at 2. 54 m/s (500 fpm)
The pleats per filter range from 12 to 60.
Model predictions are drawn into lines, while the black circle represents the observed total pressure drop at 2 points for filter types from C to K. 54 m/s (500 fpm).
For the sake of clarity, due to the fold shrinkage and expansion of this filter, the shielded resistors are excluded from the chart because their contribution is small (< 0. 5 Pa).
Error bar signal for observed flow resistance [fit]+ or -]
5% of their value
The total Model resistance within the error bar of the experimental data decreases. [
Figure 12:
The modeling results in Figure 12 support the general trends previously published regarding folding filters.
The resistance and volume count chart clearly shows the lowest resistance available (LOR)
Corresponding to the optimal number of pleats.
When the pleat count increases, LOR appears due to the trade-off between the medium resistance and the viscous resistance.
This chart also confirms Chen's claim to a certain extent that cutting-edge blockage can be ignored;
However, FM1 is a thin medium (~0. 5 mm)
The same requirements cannot be made for all media types.
A new feature of the model is the inclusion of a unique term for housing losses.
Previous studies often ignored the impact of the house, or simply masked its impact due to the simple combination of house loss and geometric loss. This has a two-
From the perspective of filter design, folding is not good.
First, the enclosure resistance is incorrectly attributed to other geometric design parameters such as flatness or flatness spacing.
This artificially increases the actual impact of these geometric parameters, resulting in errors in design estimates.
Second, the nature of house resistance is different from that of other geometric losses.
In the range of parameters explored, the structural pressure drop is basically a fixed resistance, and its effect will not change with the volume count.
The resistance of all other geometric shapes increases with the increase of pleats.
Due to the addition of the grating loss, their resistance increases slightly, which becomes more distorted as the pleats change.
By identifying and separating the contribution of the grating, the model provides a better understanding of a single resistor, allowing for enhanced analysis, improved design, and improved performance.
One such design improvement is the cancellation of structural houses.
If the same filter can be fully constructed without a shell, the total pressure drop at the optimal pleats can be reduced by 30%.
However, due to the elimination of the grating, the structural stability of the filter may be affected.
This is especially true because most filters are loaded with dirt until the final pressure drop reaches 249 Pa.
A simple solution is to add a wire mesh before and after to improve stability.
Since the wires are mainly open gaps, the net resistance effect is similar to a slight increase in the medium constant.
Second, a similar design improvement is to eliminate the front grating only.
The rear grating used in conjunction with the screen should be sufficient to support the filter medium.
Removing the front gate will reduce the overall initial resistance by a net 15%.
Accurate models can also identify a variety of design strategies to minimize material costs, minimize energy consumption, or maximize the service life of the adsorbent
The filter is embedded while maintaining acceptable initial pressure drop.
Figure 12 shows the presence of shallow water valleys between 27 and 47 folds, highlighting these design objectives.
In this valley, the initial pressure drop hovers near the resistance of 62 Pa.
At the low pleats end, a 27 pleats filter can be constructed that will run under sufficient pressure drop without generating higher production costs due to increased material costs.
This is especially useful for filters that use expensive absorbent or catalyst materials.
By increasing the number of pleats to 36 pleats, the most energy-efficient filter can be made;
However, it should be noted that if these gas filters are loaded with debris, the overall energy consumption will be greatly affected.
The high-end of the Valley offers a filter with a maximum usable filter area and an adsorption load without fully increasing the initial pressure drop.
The ability to locate and work in this valley proves the utility of an accurate pressure drop model for filter designers.
The position of the optimal pleats although it can be used as a general heuristic algorithm, the optimal pleats do not simply exist in the case of equal media and geometric resistance.
For example, the optimal number of pleats in Figure 12 is 36 pleats, however, the medium and pleats resistance are equal at 38 pleats.
When the change rate of the total pressure drop relative to the pleat count is zero, the most unlikely resistance and the best pleat count actually occur.
Since equation 9 is composed of polynomials, the model can be decomposed into individual terms, and it is easy to calculate the first-order derivative off the pleats count. [[
Partial derivative[DELTA][P. sub. F]/[
Partial derivative][P. sub. C]]= [[
Partial derivative]([rho][K. sub. G][V. sub. 1. sup. 2])/[
Partial derivative][P. sub. C]]+ [[
Partial derivative]([1/2][rho][K. sub. C][V. sub. 3. sup. 2])/[
Partial derivative][P. sub. C]]+ [[
Partial derivative]([1/2][rho][K. sub. E][V. sub. 3. sup. 2])/[
Partial derivative][P. sub. C]]+ [[
Partial derivative]([1/2][rho][K. sub. P][V. sub. 3. sup. 2])/[
Partial derivative][P. sub. C]]+ [[
Partial derivative(A[V. sub. 4])/[
Partial derivative][P. sub. C]]+ [[
Partial derivative(B[V. sub. 4. sup. 2])/[
Partial derivative][P. sub. C]](13)[[
Partial derivative[DELTA][P. sub. F]/[
Partial derivative][P. sub. C]]
= Team 1 Team 2 team 3 Team 4 Team 5 Team 6 (14)
Contribution of grating (Term 1)
The first derivative is a zero derivative because it is not a function of the pleat count.
First derivative of viscosity/geometric effect (
Terms 2, 3 and 4)
The resistance of the media is always positive (Terms 5 and 6)
The Count of pleadings has always been a negative first derivative.
Equation 14 can give equation 15 from the left
At the best number of pleats, the hand side is equal to zero. -[[1/2][rho][[[
Partial derivative([rho][K. sub. C][V. sub. 3. sup. 2]+[K. sub. E][V. sub. 3. sup. 2]+ [K. sub. P][V. sub. 3. sup. 2])]/[
Partial derivative][P. sub. C]]= [[[
Partial derivative(A[V. sub. 4]+[BV. sub. 4. sup. 2])]/[
Partial derivative[P. sub. C]](15)
Figure 13 is a graphical representation created by taking the first derivative of the model, as shown in equation 13.
Calculate each derivative while keeping the filter size, surface speed and media properties unchanged and changing the pleats to 12 to 70 pleats.
Modeling parameters for creating figure 12 (
FM1 media control, 2.
Surface speed 54 m/s, size 508x25mm)
Same as used to create figure 13.
Figure 13 clearly shows the balance between viscosity and media
Leading resistance. [
Figure 13:
Conclusion a strict model was established according to the physical properties of the medium and the design of the pleat filter.
Model pressure drop estimates for 20 different single filters are within [range]+ or -]
5% of the observed resistance value.
Since the model does not use non-transferable parameters, accurate pressure drop prediction can only be based on empirical data on the thickness and permeability of the medium obtained.
The model is consistent with previous research published in the field.
Model parameters such as pressure drop, fold height and fold count directly affect operating costs, area of available media, and performance.
Models containing these influential design parameters and variations can be used as design tools for filter units. At a fixed-
This model can be used to calculate the minimum available resistance and the corresponding optimal volume for a given medium.
In HVAC systems with fixed wind speed and allowable pressure drop, the model can predict the maximum filtration area and the load of the adsorption agent.
It can be further used as a design tool for media construction.
The preferred medium properties relative to permeability and thickness are calculated to achieve the ideal operating conditions.
The ultimate benefit of the adsorption filtration design is the increase in available adsorption agents, the reduction in material costs or the reduction in operating energy costs.
Admitted that the study was in the United States. S.
Army tacom lcmc (contractW56HZV-05-C-0686).
Name A = Media constant, Pa * s/m [A. sub. Free]= free area, [m. sup. 2][A. sub. i]
= The area of point I ,[m. sup. 2][D. sub. W]
= Pipe width, m [F. sub. HD]
= Hydraulic diameter of filter, m [F. sub. W]
= Filter width, m accept Ryan A on July 31.
Sothen is a graduate research assistant at the Department of Chemical Engineering at AL Auburn University. Bruce J.
Tatarchuk is a professor of chemical engineering at Auburn University and director of the municipal center for the manufacture of microfibre materials.